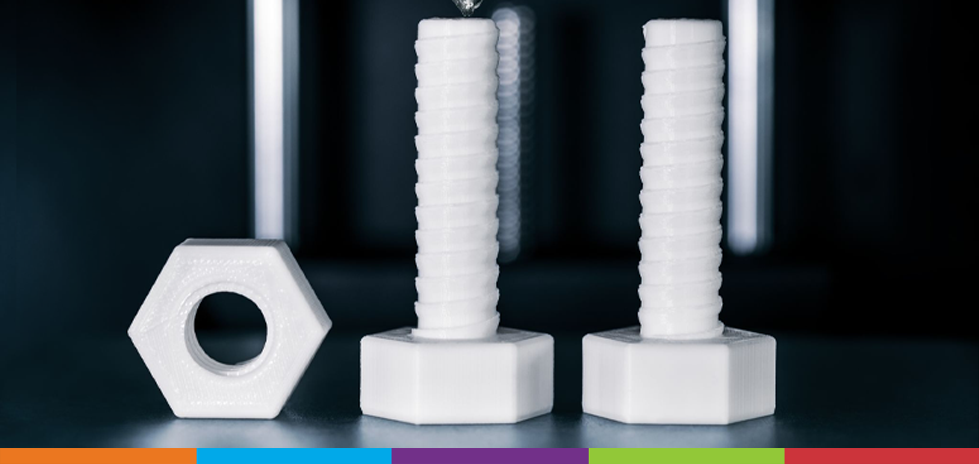
3 个步骤:从原型设计到生产
从原型设计到生产,Optimas Solutions 帮助全球制造商提高产量并降低各个领域的成本。
我们的内部设计工程师使用 3D 打印和棒料车削等专业原型设备,与客户从产品开发到生产线进行合作,以确保他们的零件在我们工厂生产之前得到优化使用。 冷锻设备 在美国和英国。
从原型设计到开发和生产高品质紧固件,我们仅采取以下三个步骤:
1. 3D打印
Optimas 的专业设计工程师根据行业特定要求与客户在现场或根据项目情况合作,打造可靠的紧固解决方案。
3D 打印是工程师用来快速检查紧固件在应用之外的设计和尺寸的一种方法。3D 打印机可以在一天内制作定制零件的原型,这意味着这是一个高效的过程。
3D 打印还可以实现产品的分步组装,从而提高设计过程各个环节的可视性。制造商通常需要专门的部件,而 3D 打印可以让设计师制作出精确、几何形状复杂的原型。
3D 打印创建的原型也是有形的,功能齐全,可以准确确定部件的应用适用性,从而优化其设计。如果该部件被认为不合适,可以在第二天打印一个新的原型。3D 打印也比传统的原型制作方法更便宜,因为它只需要很少的人力资源,而且产生的极少量废物可以完全回收利用。
2 – 棒材车削
通过 3D 打印优化产品设计后,可以通过棒料车削快速地对零件进行小批量的原型制作。
棒料车削提供了有关零件机械性能的重要信息,包括其抗拉强度、屈服强度和延展性,以确保其在使用时性能良好且无缺陷。棒料车削不仅可以实现高效、准确的原型制作,而且对于小批量零件来说无需工具成本。
棒料车削还具有较高的表面质量和精确的尺寸,避免了生产过程中后期的过度加工。
我们的工程师通过了IATF 16949和ISO 9001:2015认证,并使用质量规划系统在整个生产过程中有效地诊断、纠正和减轻流程或产品风险。
3.冷锻
一旦零件通过这个严格的测试过程进行了优化,它们就可以在我们的专业冷成型设施中进行大批量生产。
冷锻制造 大规模生产特别耐用的紧固件,经验丰富的冷成型机制造商可以将工作精度提高到 0.02 毫米以内,这意味着您一定能收到完全符合您的设计的专业、高品质零件。
Optimas 位于英国德罗伊特威奇的 Barton Cold-Form 工厂与产品产量极高的制造商合作,但由于 29 台 Nedschroef、Sacma 和 Nakashimada 冷镦机全天 24 小时运行,Barton 非常适合大规模生产。一台冷镦机每天可以生产数十万件产品,这比其他形式的制造(如热锻)要高得多。
我们在满足客户定制紧固需求方面拥有 90 多年的经验。我们的综合工程和制造能力可以帮助您提高产品产量和质量。无论您需要标准紧固解决方案还是工程紧固解决方案,我们的工程和行业专业知识与我们的合作方式相结合都可以优化您的产品性能。 立即联系我们 最大限度提高您的生产效率。