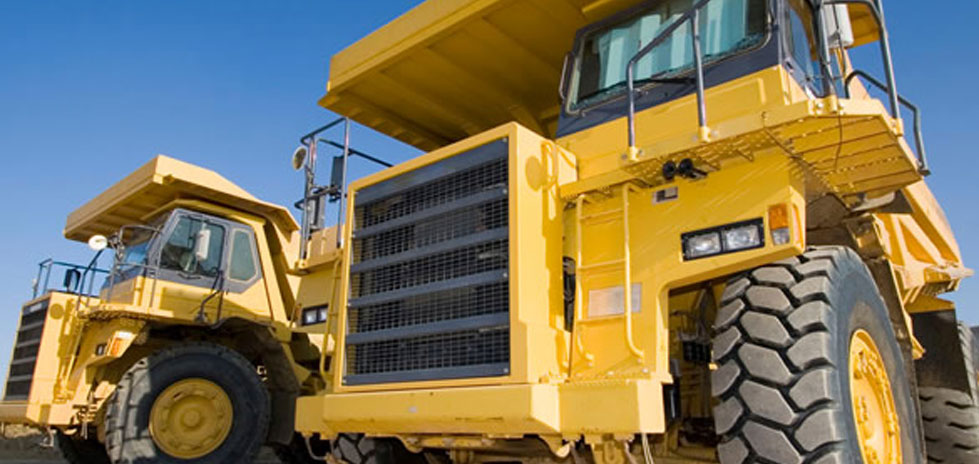
Gli autobus elettrici compositi di nuova generazione viaggiano con dispositivi di fissaggio Optimas
La Cina, in particolare, è stata una delle prime ad adottare gli autobus elettrici, ma ora la tendenza sta crescendo in tutto il mondo. Con una maggiore attenzione legislativa e pubblica sui livelli globali di emissioni, sulla qualità dell'aria nelle aree altamente popolate e sul dibattito intorno ai propulsori diesel tradizionali, i propulsori elettrici offrono ora un'alternativa praticabile per la gestione dei trasporti pubblici senza influire negativamente sull'ambiente. Con i moderni miglioramenti nella tecnologia delle batterie e nella gamma dei veicoli, il bus elettrico sta guadagnando slancio.
Il passaggio a una nuova generazione di propulsori presenta alcune sfide considerevoli per i produttori di autobus OEM. Innanzitutto, a differenza di un propulsore a benzina o diesel, i propulsori elettrici trasportano enormi quantità di corrente elettrica. Pertanto, i componenti di questi veicoli devono essere adeguatamente isolati per garantire che non si verifichi la conduzione ad altre parti del veicolo e invertire la polarità.
La seconda è la questione del peso. Con una gamma limitata tra le stazioni di ricarica, gli autobus elettrici devono essere il più leggeri possibile per fornire la massima efficienza in movimento. Quando si tiene conto dei passeggeri, è chiaro che ridurre al minimo il peso anche del componente più piccolo è di fondamentale importanza.
Inserisci i compositi. La capacità dei compositi di costruire assemblaggi adeguatamente robusti con un peso ridotto li ha visti diventare un punto fermo delle auto da corsa in tutto il mondo. Tuttavia, quando applicato ai veicoli elettrificati, il peso ridotto non si traduce solo in maggiori prestazioni, ma anche in una maggiore portata.
La terza sfida è lo sviluppo di una base di conoscenze sufficiente per creare una piattaforma elettrificata completamente nuova. L'industria sta attualmente attraversando un paradigma verso l'elettrificazione, quindi molte aziende potrebbero non avere accesso alle competenze esistenti in materia di veicoli elettrici. In termini di selezione degli elementi di fissaggio per queste piattaforme innovative, può essere difficile trovare l'esperto giusto per fornire i componenti ingegnerizzati corretti con una qualità adeguata. Soprattutto quando gli standard di produzione sono più associati alle squadre da corsa che ai trasporti pubblici.
Questo è il motivo per cui un produttore di autobus si è rivolto all'esperienza di Optimas Solutions, un distributore industriale globale e un fornitore di servizi, per aiutare a specificare elementi di fissaggio adeguati per la sua nuovissima piattaforma modulare per autobus compositi. Optimas sta rapidamente guadagnando la reputazione di fornire i dadi e le viti dietro alcuni dei veicoli elettrici più impattanti che emergono sulla scena mondiale; rendendolo il partner ideale per tali progetti. Alla fine, il produttore ha identificato la necessità di definire un innovativo Bill of Materials (BoM) dall'inizio del progetto che si adattasse al telaio composito.
Ian Larkin, Engineer Application Engineer di Optimas, riflette sul progetto: “Inizialmente ci è stato chiesto di unirci al progetto da un fornitore di terze parti, un distributore esistente di hardware per il produttore di autobus. Questo fornitore fornisce parti standard per supportare la produzione di modelli di autobus esistenti; hanno richiesto il nostro contributo per aiutare con la piattaforma di autobus elettrici. In particolare, ci è stato chiesto di aiutare a sviluppare una gamma di standard di fissaggio e identificare progetti di fissaggio speciali. Collaboriamo spesso con produttori e fornitori OEM per aiutare nello sviluppo di elementi di fissaggio, quindi ci mettiamo a lavorare con i team congiunti di ingegneria e progettazione. "
Il design del nuovo autobus è una novità per l'industria. Il telaio composito modulare del produttore del bus incorpora un ampio vano portaoggetti del modulo batteria situato sotto la scocca, accoppiato con un sistema di telai anteriore e posteriore. Questa disposizione è associata alle auto ad alte prestazioni, ma la sua vantaggiosa combinazione di una migliore distribuzione della forza su tutto il telaio e un peso ridotto si adatta perfettamente all'applicazione del bus elettrico.
"Siamo stati in grado di definire un elenco di parti standard per costruire i prototipi di autobus, che abbiamo selezionato dal nostro portafoglio globale di produttori di componenti", continua Ian. “Per raggiungere questo obiettivo, abbiamo abbinato i componenti agli standard di fissaggio per questo progetto, facendo riferimento a componenti che erano già stati selezionati per costruire i bus prototipo iniziali. Alla fine, siamo stati in grado di consegnare 162 distinte parti alla distinta materiali, incorporando dadi, bulloni, viti e rondelle. Dopo aver aggiunto queste parti in un processo di costruzione controllato, il produttore è stato in grado di produrre 5 prototipi. Successivamente, l'azienda ha lanciato sul mercato il nuovo autobus elettrico una volta completati i test.
“La specifica dei dispositivi di fissaggio per veicoli elettrici è una sfida per molti costruttori di veicoli OEM che devono affrontare attualmente, ed è una sfida che devono affrontare per assicurarsi di essere in testa alla curva del settore. Sfruttare la nostra esperienza con i fornitori di dispositivi di fissaggio nel settore dei trasporti e automobilistico significa che siamo preparati con soluzioni. Con il passaggio a veicoli a basse emissioni e completamente elettrificati, è facile dimenticare che non è solo il gruppo propulsore a subire enormi sviluppi, ma anche i dispositivi di fissaggio e gli assiemi associati. ”
Ulteriori informazioni sul nostro Servizi di ingegneria.