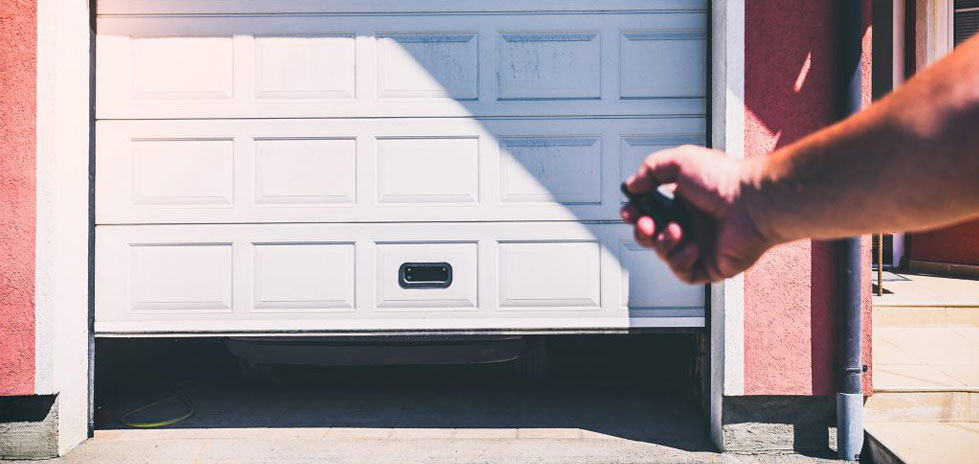
Les fixations techniques réduisent les dépenses en composants de 75% pour le fabricant de portes automatiques
Dans une économie mondiale compétitive, il est important de trouver l'efficacité à toutes les étapes de la production. De nombreux fabricants cherchent à atténuer les contraintes de la chaîne d'approvisionnement grâce à des stratégies logistiques améliorées, mais ce n'est pas le seul domaine à améliorer?
Quelque chose qu'il est possible de supprimer le stress de la chaîne d'approvisionnement en remettant en question la complexité des composants physiques commandés. En simplifiant les fixations utilisées dans un produit, l'approvisionnement en matériel est également par conséquent plus facile. En tant que distributeur mondial et fournisseur de services d'ingénierie, Optimas Solutions est capable d'identifier ces solutions. Il a récemment adopté cette stratégie pour aider l'un des principaux fabricants mondiaux de solutions d'accès automatique.
Le fabricant s'est bâti une réputation mondiale en fournissant des ouvre-portes automatiques, des télécommandes, des pièces et des accessoires. La durabilité est primordiale dans les portes automatisées, car elles doivent pouvoir fonctionner sans problème pendant de longues périodes et pendant une utilisation intensive, de sorte que l'entreprise réévalue souvent ses conceptions pour identifier les améliorations.
C'est lors du démontage de routine d'un ouvre-porte commercial automatique que l'histoire commence. Le démontage a été effectué dans le cadre d'un engagement continu envers la qualité, afin d'identifier toutes les opportunités d'amélioration des produits dans la conception existante. Ce ne serait pas un exercice infructueux. L'accent s'est rapidement tourné vers l'ensemble de freinage de l'unité de porte, qui contenait un système de ressort composé de quatre coupelles en laiton à bride retenant les ressorts de compression à un goujon fileté intérieurement. Bien qu'apparemment inoffensifs, les équipes d'ingénierie ont commencé à étudier le système, ce qui a mis en évidence certaines opportunités de développement.
La première enquête a été le choix du laiton comme matériau pour les quatre tasses. Bien qu'idéal pour les opérations dans des environnements qui pourraient potentiellement poser des risques de corrosion, il n'y avait aucune raison que le laiton justifiait l'inclusion dans une application commerciale de portes basculantes. Le reste de l'unité était en acier galvanisé, ce qui a mis le choix du laiton sous le feu des projecteurs. De plus, les coupelles étaient vissées en laiton, ce qui signifiait que le fournisseur avait souvent du mal à répondre aux exigences de production du fabricant. Cela mettait à rude épreuve la chaîne d'approvisionnement, ce qui pourrait menacer la disponibilité de la fabrication si la demande pour ce composant augmentait.
Tim Day, ingénieur d'applications chez Optimas, développe la méthodologie suivante: «Après quelques recherches, nous avons constaté que les tolérances fournies par l'usinage du composant n'étaient pas cruciales pour cette application. Par conséquent, nous avons recommandé un remplacement en acier à faible teneur en carbone formé à froid par l'un de nos fournisseurs personnalisés, avec une finition galvanisée au zinc et au chromate transparent, qui serait adéquate pour la protection contre la corrosion pendant l'expédition et la manutention des pièces.
La spécification d'un composant formé à froid a fourni une multitude d'avantages. L'utilisation d'un gabarit à matrices multiples, qui ne nécessite aucun traitement secondaire après le formage, a signifié une efficacité accrue de la production. Le formage à froid a également réduit le gaspillage, fournissant une méthode plus respectueuse de l'environnement pour produire le composant requis. Cela est dû au fait que la matière première est pressée sous haute pression dans la filière, ce qui ne produit aucun déchet. La fabrication pourrait également commencer sans nécessiter de modifications de conception de l'un des composants de couplage, ce qui a ajouté de la valeur lors de la mise en œuvre.
Tim poursuit: «En choisissant une alternative en acier, nous avons réussi à réduire le coût de chaque composant individuel de 75%, ce qui a ajouté de la valeur au fabricant de portes automatisées. Un processus de fabrication simplifié pour le composant a également allégé la pression existante au sein de la chaîne d'approvisionnement, ce qui a directement répondu aux risques que le composant d'origine posait pour la disponibilité. En conséquence, nous pourrions apporter de la valeur et renforcer la chaîne d'approvisionnement existante grâce à l'introduction d'un composant unique. »
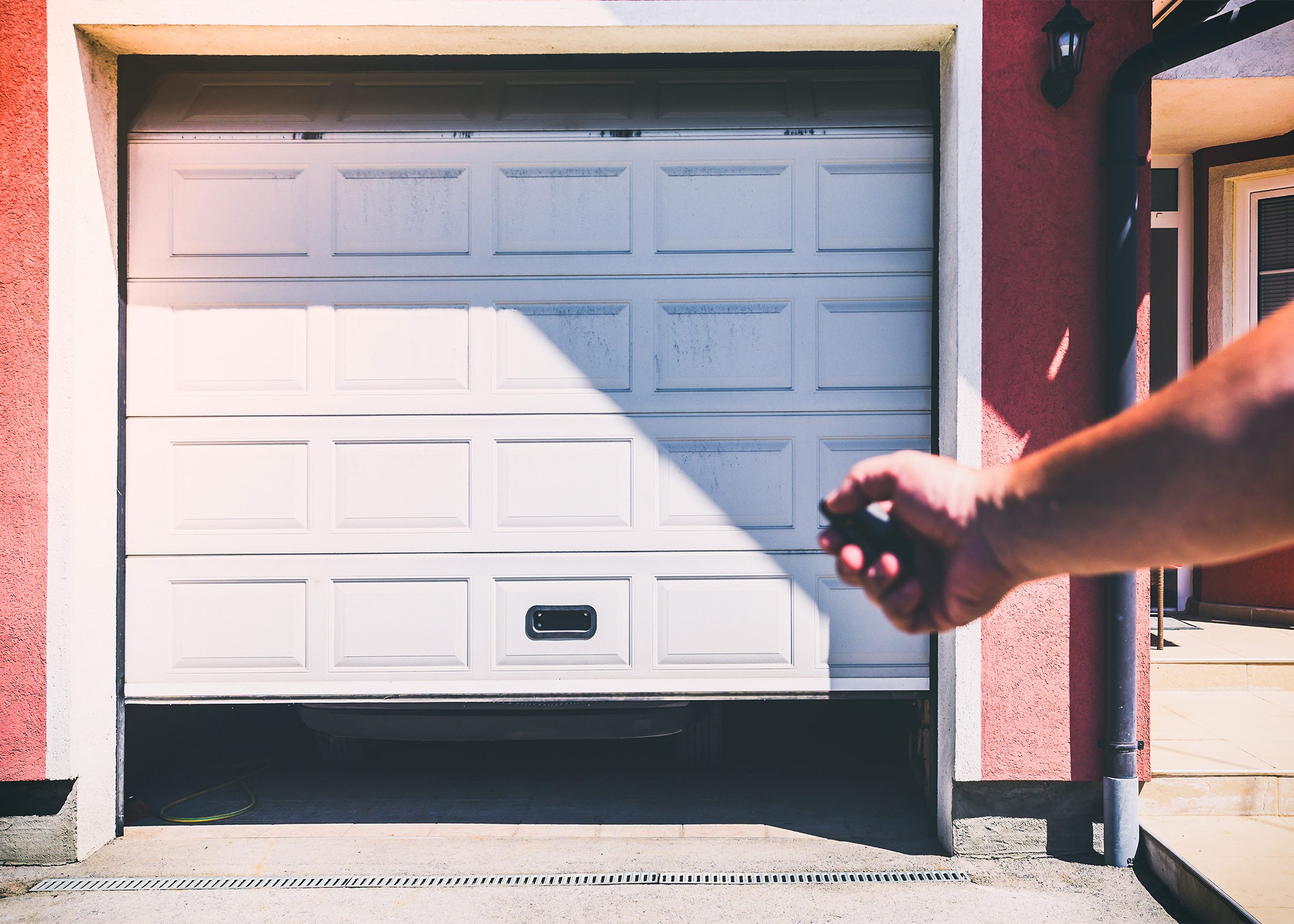
Porte de garage PVC. Télécommande à main pour fermer et ouvrir la porte de garage.
Satisfait de la solution proposée, le fabricant a effectué les tests de cycle de vie obligatoires que tous ses produits doivent effectuer. La porte a été actionnée en continu en marche avant et arrière pendant une période de temps prolongée. Cela a permis aux ingénieurs d'évaluer tout problème concernant la fatigue ou la corrosion pendant l'utilisation, toutes les préoccupations clés pour un produit qui serait fortement utilisé dans une application commerciale. Une fois les tests terminés avec succès, la coupelle en acier à faible teneur en carbone a été intégrée à ce modèle de porte basculante.
En conclusion, Tim déclare: «En engageant Optimas en tant qu'expert externe des fixations, le fabricant a pu résoudre simultanément un certain nombre de problèmes liés à la chaîne d'approvisionnement et aux applications. En adoptant cette approche intégrée des fixations, il peut être simple d'identifier les composants spécifiés, de trouver des alternatives et de mettre en œuvre la solution choisie avec très peu de perturbation des opérations existantes. Je pense que toute personne associée à la fabrication à grande échelle peut en voir les avantages. »