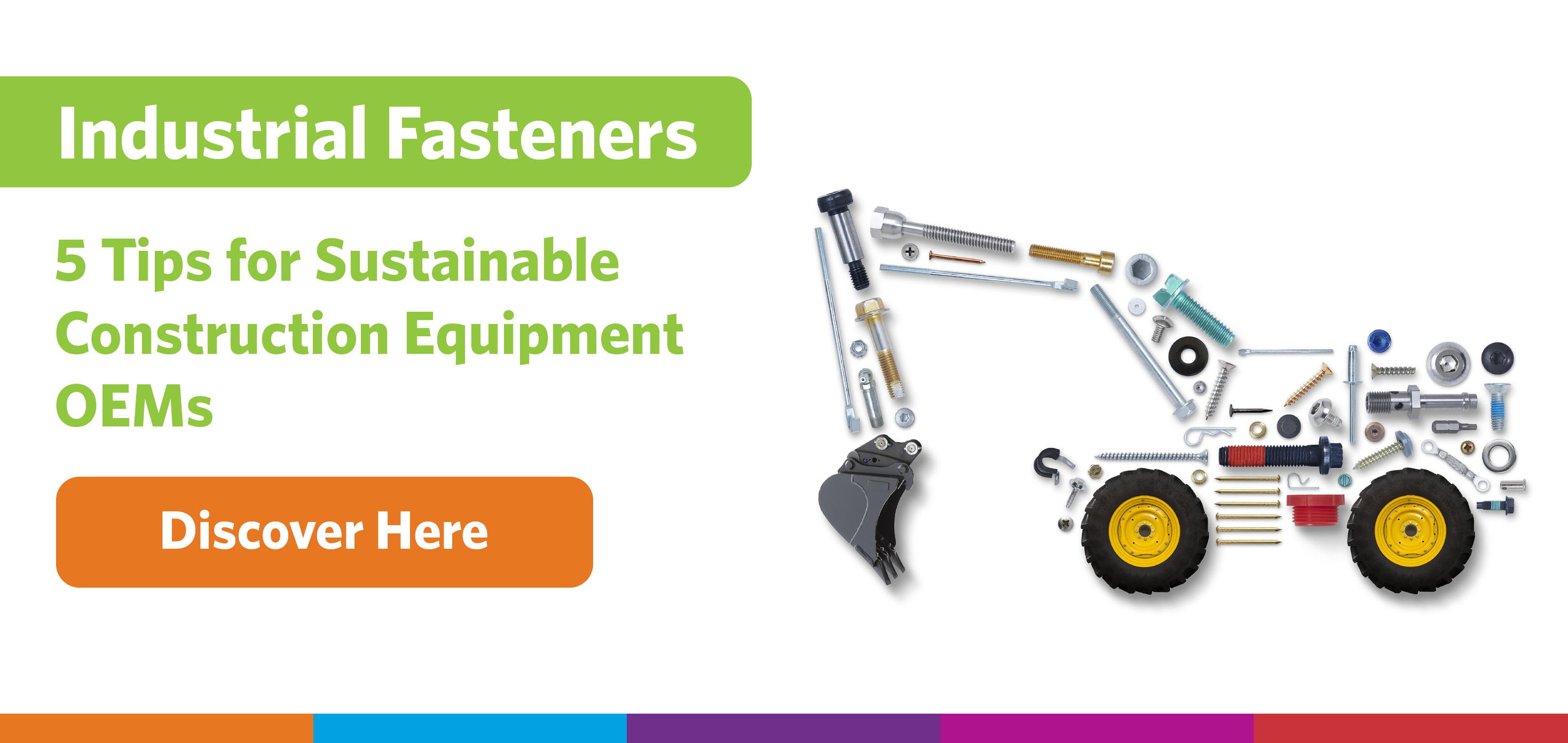
Industrial Fasteners for Sustainable Construction Equipment
The construction industry is on a pivotal journey toward sustainability and Original Equipment Manufacturers (OEMs) have a critical opportunity to lead this transformation by re-evaluating their choice of sujetadores industriales.
With mounting pressure to reduce environmental impact, comply with stricter regulations, and achieve long-term cost savings, the time for change is now. The UN’s 2023 global status report reveals that the building and construction sector is falling short of decarbonization goals for 2050, highlighting the urgency for action.
For construction equipment OEMs, optimizing manufacturing processes—including the selection of industrial fasteners—can significantly contribute to sustainability efforts and support the electrification of equipment. Below are five key strategies to help OEMs make impactful changes in their fastener choices.
1 – Weight
For OEMs aiming to electrify their products, considering the weight of industrial fasteners is crucial. Using industrial fasteners made from high-strength alloys can help reduce weight, which in turn enables the final product to demand less energy to operate, which improves both equipment performance and battery efficiency.
2 – Strength
Industrial fasteners must meet high tolerance and vibration demands, bearing loads between 65-90% of their yield strength to avoid loosening or breaking during installation and use. Construction equipment OEMs should consider utilizing cold-formed industrial fasteners, because the cold-forming process maximizes the fasteners’ metallurgical properties and structural integrity, prioritizing part strength and durability, which is crucial for equipment in the construction industry.
3 – Corrosion
Construction equipment encounters moisture, harsh weather conditions and chemicals, so the industrial fasteners used must be highly corrosion resistant. Materials such as aluminum, stainless steel and titanium provide excellent yield strength and are highly resistant to corrosion. Therefore, these are the materials construction equipment OEMs should look for in the industrial fasteners they use in their electric products.
4 – Thermal Conductivity
Electric construction equipment can generate a significant amount of heat during operations. If the product’s fasteners are not optimized for use, then this heat can transfer to critical components, risking poor performance and low battery life. Industrial fasteners made from aluminum help dissipate the buildup of heat in electric construction equipment and ensure the working temperature stays at an optimal level.
5 – Sustainability
As the industry pushes for reduced environmental impact, sourcing fasteners from eco-friendly manufacturers strengthens OEMs’ commitment to sustainability. Optimas’ cold form manufacturing in the UK and US prioritizes sustainable practices, resulting in minimal waste and a lower carbon footprint.
Optimas can provide a wide range of lightweight, corrosion-resistant, high-strength materials to optimize your construction equipment. Committing to electrification not only helps OEMs produce more sustainable products but also requires adopting new standards and best practices. Adhering to consistent standards ensures that every partner, supplier, worker and stakeholder understands and aligns with the mission.
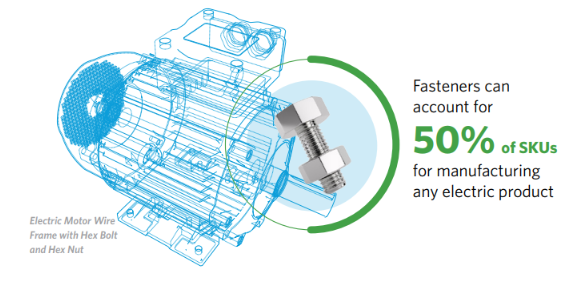
Fasteners can account for up to 50% of SKUs in manufacturing electric construction equipment, making it vital for OEMs to choose the right fasteners to maximize efficiency.
Our application engineers at Optimas are ready to support your product builds from conception to production. Contact our experts today to see how we can optimize your construction equipment and products across various industries.
Learn how Optimas achieved a 30% assembly cost reduction and 10% weight savings for a new excavator line. Stay updated with the latest news, resources, and insights by subscribing to our LinkedIn newsletter.
Solicite una copia de nuestro EBook sobre Electrificación
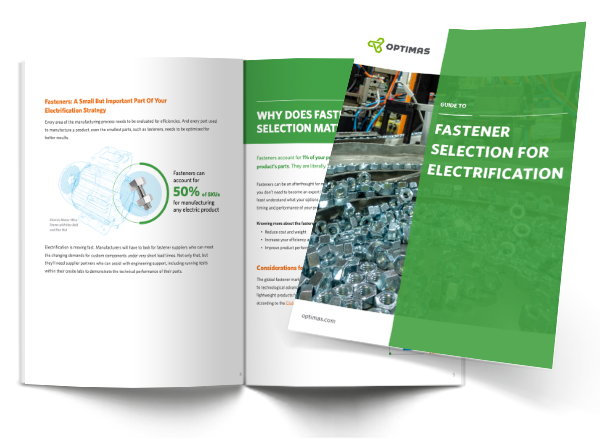