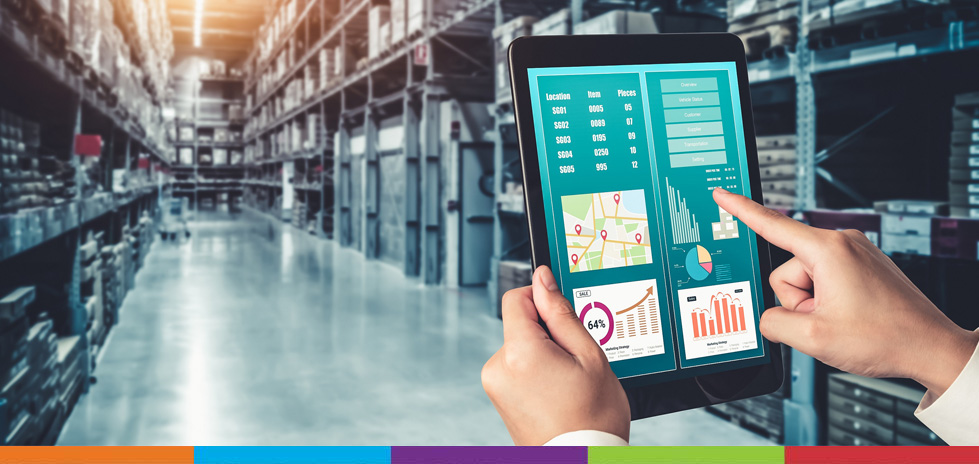
VMI: Productivity and Cost Reduction
In a time of increasing supply chain instability and rising inflation, it’s crucial for businesses to reduce their spending and maximise efficiency. One way to do so is through the use of a VMI (Vendor Managed Inventory). The last few years have seen an increase in the popularity of VMIs, as businesses seek to reduce their number of suppliers and instead opt for streamlined and cost-effective organisation.
As manufacturers ourselves, we’re constantly looking for improvements to our production process, so we understand the position our partners are in.
What are the key benefits of Vendor Managed Inventory?
A VMI ensures products are delivered to the right place at the right time through improved data visibility, resulting in improved productivity in addition to:
Cost Reduction
Current financial instability means that businesses are having to reassess their outgoings, and there are numerous financial benefits of using a VMI. Firstly, it reduces manpower needed by your business. In a supply chain, the parts themselves make up only 15% of the cost, while the human resources required to select, manage and process those parts cost 85%.
In addition, using a VMI can simplify and reduce the cost of the ordering process, all while reducing your TCO (Total Cost of Ownership), as the vendor assumes the cost and associated risk of managing your supply chain. Partnering with a single vendor also diminishes possible excess spending by collating your parts into a single, automated order.
Streamlined Production
The current political climate is buckling global supply chains, so it’s more important than ever for businesses to control their stock levels and avoid waste. VMIs use various advanced technologies to automate both simple and complex processes, removing costly and unnecessary steps.
A VMI service provider can also source products for you, from a diverse range of suppliers. Some experts suggest that the cost for a business to add in just ten extra suppliers every five years is more than $1 million, but a VMI handles that for you. Each part is then ordered, delivered, stored and replenished automatically, as and when you need it.
Types of VMIs at Optimas
Optimas has numerous VMI solutions for your business. Our systems use the latest technology to automate inventory replenishment, ensuring productivity and saving you money.
JIT Systems
- Our JIT systems provide a secure, cloud-based platform that processes orders from any OptiTech VMI solution and allows you to access customised, real-time reports for greater transparency into your fastener inventory and consumption data.
OptiScale
- OptiScale uses the latest weighing technology to measure your inventory status in real-time, down to the part level quality in a bin. Embedded sensors monitor the weight capacity, automatically triggering orders based on pre-defined min/max levels and reorder/unit pack sizes. Stock levels can be accessed 24/7, and OptiScale can be configured into a bin, shelf or container.
OptiRack
- OptiRack uses advanced RFID (radio-frequency identification) technology to automate inventory replenishment. When an empty bin is placed on an RFID mat on the rack shelf, it detects the chip embedded in the bin label, and wirelessly triggers an order. OptiRack can be set up in any designated area, whether it be a supermarket, area rack or at the point of use.
OptiZone
- OptiZone uses advanced RFID technology to automate inventory replenishment. An RFID antenna points to a designated area, a pallet, cage, gaylord container or bulk area. When an empty bin is placed in that area, the antenna detects the RFID chip embedded in the bin label and then wirelessly triggers an order.
OptiDrop
- OptiDrop uses RFID technology to automate inventory replenishment, but does so by scanning a unique card with an RFID embedded chip in a bin. When the bin is empty or low, simply remove the card and replace it inside the OptiDrop box to wirelessly trigger an order. OptiDrop can be placed at any location inside the plant.
OptiBeam
- OptiBeam uses the latest scanning and barcode technology for easy inventory replenishment. Our cellular-enabled scanners allow both Optimas the customer to check inventory levels and send orders instantly. The scanner includes auditing software so you can search parts, validate bin location and set optimal reorder/unit pack sizes.
Here at Optimas, we’re dedicated to efficient inventory management, and we’d be as invested in your success as you are. To find out more about our VMI solutions, or to speak to one of our experts, you can do so here. Consider working with us to lower your costs and streamline your supply chain.