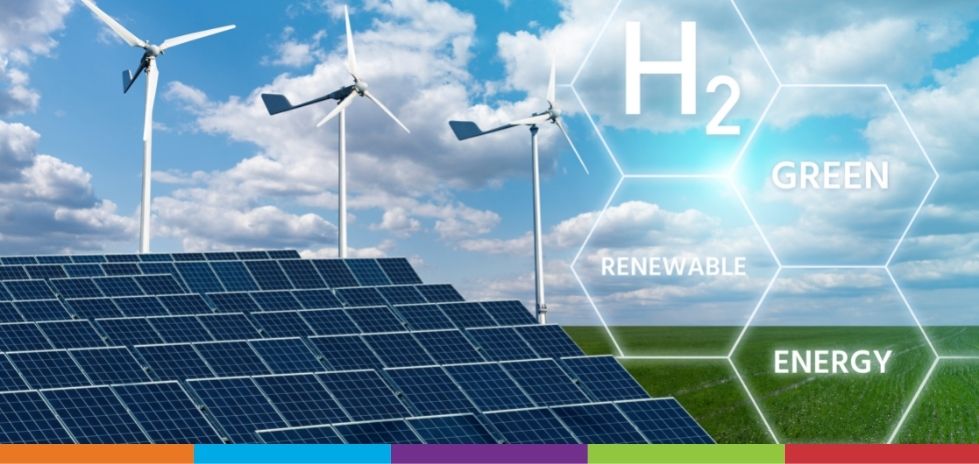
The Future of Industrial Processes Is Electrification
Manufacturing electrification is having a moment right now, and it goes way beyond vehicles. Many manufacturers are beginning to embrace electrification as a practice. According to a Deloitte study, 70% of executives surveyed said they plan to embrace the electrification of industrial processes.
There’s a reason for this shift.
According to McKinsey projections, renewable energy sources are likely to produce more than half of the world’s electricity by 2035. And because renewables cost less in the long run, electricity prices will drop. This dip — combined with the rising expectation of renewability in the industry — will cause demand for electric-powered products (e.g., automobiles, space heaters, farming machinery) to soar.
Consequently, renewable energy is now accepted as more than just a passing fad. Manufacturers feel the urgency of moving toward the electrification of industrial processes and are beginning to strategise accordingly. But as they embrace the idea of electrification, the challenges of creating sustainable manufacturing practices will emerge, including:
- New Supply Chain Processes to Install: Manufacturers might need to change the scale and agility of their approaches to keep pace with the demands of electrification. They may also need support for their new supply chains.
- New Materials to Understand: Making electric products may require teams to acquaint themselves with new terminologies. Using renewable energy in manufacturing will change the materials we need, bringing unique strengths, weaknesses, and tolerances.
- Newer, Stricter Regulations to Follow: The move to renewable energy creates a need to acknowledge and adhere to more stringent governance. Manufacturers who embrace electrification need to be ready to take compliance seriously.
If manufacturers want to reap the benefits of renewable energy, these roadblocks need to be cleared.
The Current State of Manufacturing Electrification
Industries now understand how essential renewable energy is to the future of manufacturing. And it’s a realisation that comes with some immediate forecasts.
For starters, industry leaders are feeling pressure to shift their manufacturing practices. Changing legislation and the rise of environmental concerns each make it more challenging to maintain the nonrenewable status quo. This has caused manufacturers to review their practices and industry leaders to publicise their own energy usage and make pledges to reduce greenhouse gas emissions.
Plus, the inherent business value of lowering emissions is making manufacturers organic advocates of manufacturing electrification rather than just circumstantial ones. Part of this about-face stems from the increased transparency around environmental, social, and corporate governance (ESG) criteria illustrating the cost-benefit ratio of investing in electricity.
The manufacturers who already have their sights set on renewable technology are equally aware this shift will require a new array of materials and methods to keep their supply chains streamlined. They’re also willing to deconstruct existing infrastructure and rebuild it to serve their new electric output needs.
This last point is probably the one most likely to scare new adopters. The perceived upfront costs of electrification could overwhelm, especially when combined with a perceived lack of knowledge and expertise. That’s why it’s so vital to find supply chain partners that can ease the pressure of sourcing and working with new materials.
Keeping Electric Manufacturing Costs Down
The necessary financial investment (and perceived costs) of transitioning to manufacturing electrification must be addressed to move forward confidently and successfully. Here’s a look at the most significant cost roadblocks manufacturers are likely to face:
- Longer Research-and-Development Periods: Transitioning to new product designs and materials and learning to work with new teams and individuals will take time. If this R&D process is not adequately streamlined or budgeted for, costs will balloon as the project persists. If their short-term ROI isn’t bearing fruit, some company leaders will feel the pinch of this long-term thinking — and it will be challenging to craft a future landscape of lower carbon emissions if the present moment is financially tricky.
- Need for Maturer Technology and Production: To see how electrification affects businesses and consumers, the industry will need time to become more seasoned. It will take time for production lines and supply chains to settle into measurable patterns, and it will also take time for initial costs to prove their worth. With venture capitalists beginning to add clean energy technology to their portfolios, we’ll have to wait to see the exact impact of all this investment.
- Cost-Cutting Initiatives Needing to Take Effect: Government bodies are beginning to get their acts together and plan for a transition to clean energy. The U.S. Department of Energy has pledged to cut solar energy costs over the next 10 years, and it is making sizable investments in the development of technologies like the perovskites and cadmium telluride used to make thinner solar cells. These are exciting innovations that will speed up the growth of electrification. But for manufacturers to immediately benefit, they’ll have to cut costs as they make their initial commitments to manufacturing production optimisation.
Spending is a prohibitive factor for many manufacturers looking to adapt to the clean energy future, but that shouldn’t be the case for long. We need to find cost-effective electrification measures that can soothe these concerns.
Lessons From Existing Manufacturing Industry Disruptors
In an era of rapid growth, learning, and nascent technologies, it will be the manufacturing industry disruptors that show us what is possible. Past examples bear this out.
Consider the case of Woolworths, for example. When the retailer took the risk of rolling out the first closed-door fridges, the upfront investment was huge. But the company should end up saving more than $10 million thanks to the effort.
In electrification’s case, pilot commitments show how companies taking costly risks are already seeing massive payoffs. Plus, they are giving the next generation of manufacturers the ability to learn from their pioneering projects.
Tesla’s investment in electric vehicles almost created the manufacturing electrification demand that followed. Elon Musk paved the way for his competitors to invest in their own R&D, and his success encouraged others to take the industry seriously and begin their own innovations. This is why actually being a disruptor is such a risky business; your product could lose value if it inspires others to follow the trend.
However, looking at how Tesla created the space for competitors to follow is useful when considering what we need to make manufacturing electrification happen.
We can see the importance of distribution networks. Any electrification of industrial processes is going to require a network of specialist minds coming together. New use cases like farm machinery will require industry partnership, combining farmer insights with engineering innovations and support for new infrastructure.
Disruptors also highlight where the demand is. The birth of electric vehicles uncovered a crowd of consumers pushing for change. People are developing their values, and the demand for sustainable business practices is growing. This is forcing manufacturers to evolve and communicate those shifts to their audiences.
These lessons from the electrification pioneers are only the tip of the iceberg. As other industries embrace this shift, there will be no shortage of disruptive changes that ultimately benefit everyone.
Industries Primed for Electrification Disruption
One of the most exciting moments in the electrification of manufacturing processes comes just before innovation. There are many industries that are on the cusp of electrification, ripe for bold disruptors and forward-thinking adopters to shape the near future. They include:
- Transportation
From passenger vehicles to heavy-duty trucks and commercial vehicles, this form of electrification is the next natural step being encouraged by consumers and businesses. The transportation industry is notoriously slow to change, but it has turned on its heels quickly in recent years due to developments in battery performance and the cost of materials. All of these changes have been led by the example of electric passenger vehicles. However, 98.3% of heavy and medium trucks in Europe still run on diesel, according to the European Automobile Manufacturers’ Association. In short, change is welcomed.
- Machinery
To create the infrastructure needed to transform something like the automobile industry, we need a lot of machinery and many moving parts. The rapid development of electric vehicles allows us to start creating aligned machinery. Battery-electric versions of old industrial staples are beginning to emerge. Think construction vehicles: manufacturers of excavators, like Hitachi and Volvo, are switching to zero-emission machinery.
- Commercial Buildings
Vehicles and machines aren’t the only territories where electrification can be transformative. One of the next battlegrounds for electric evolution will be construction. There will be 40.5% more commercial floor space available by 2050, according to predictions by the Center for Climate and Energy Solutions. But once commercial buildings are in place, they tend to stick around for centuries and produce a shocking amount of emissions. The time is now to adjust our building processes and introduce electrification.
- Wind and Solar
The key catalyst for the development of electrification in manufacturing is the lowering of costs, and this is precisely what has happened in the fields of wind and solar. The prices of parts, modules, and materials have dropped; the cost of building a wind turbine, for example, has fallen 58% over the past decade. This has made wind and solar technology possible for people, and this snowball effect could lead to carbon neutrality by 2050.
- Agriculture
It started with electric vehicles and construction machinery, but the move to electrification in the agriculture industry is diversifying. Manufacturers like John Deere are working on tractor models with autonomous functions, and others are working on solar solutions to driving machinery like weed-pulling robots. With agriculture accounting for 5% of industrial energy consumption, manufacturers are feeling the pressure in a space ripe for disruption.
- HVAC-R
It might not be as sexy as an electric sports car, but air control and refrigeration management are two manufacturing areas with the biggest potential for transformation. Refrigeration has been named a “super pollutant,” and its renovation has been identified as the climate solution most urgently needed. There’s also the reality that the world is heating up, which means drastically more air conditioning will be needed by 2050 to keep pace — it’s time for a refrigeration revolution.
With the climate changing by the day, regulatory bodies and governments finally acting, and consumers developing firm stances on clean energy and zero carbon emissions, manufacturing needs to reckon with the immediate future. Electrification is emerging as the next industrial revolution — and it’s time to commit.