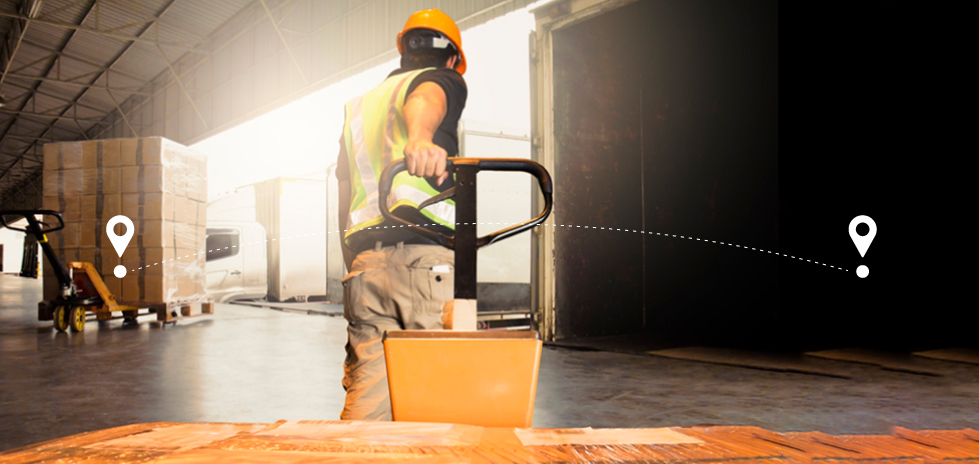
5 Benefits + 4 Steps to Re-Shore Your Supply Chain
COVID-19 is not the first global event to disrupt supply chains and it certainly won’t be the last. Just as building owners prepare for a coming hurricane, managers should prepare their supply chains to weather disruptions. Many experts advise that re-shoring supply chains to the United States is one way to minimize risk and increase stability in the face of uncertainty.
Who Leads The Way To Re-Shoring Supply Chains?
I’ve worked for decades in the automotive OE, aftermarket, heavy-duty, and industrial markets, and I’ve witnessed many automotive manufacturers undergo initiatives to localize their supply chains. BMW and Toyota come to mind in particular. In general, large manufacturers like these have led the way and many of their suppliers have followed them.
For manufacturers that are just considering bringing their supply chains back onshore in the U.S, here are some things to consider.
Offshore Supply Chains & Total Cost of Ownership
According to the Re-shoring Initiative, 60% of manufacturers ignore 20% or more of the total cost of off-shored products.
From what we have seen so far of the 2020 pandemic and its aftershocks, supply chains that were built primarily on low cost, single source, and low inventory were the least equipped to deal with massive disruptions.
Cost-myopia is the pre-COVID-19 model and manufacturers need to start their strategies for Post-COVID resiliency by thinking about Total Cost of Ownership.
My customers have heard me say that a lower piece price doesn’t do you any good if you can’t get the parts.
And, if you do find yourself in this position, you’ll spend extra money on safety stock, shipping, and logistics to fix the problem.
In terms of this ongoing crisis, the most resilient supply chains are the ones with a dual sourcing strategy that helps them source from multiple regions. But what about bringing it 100% onshore? What can you expect?
5 Benefits of an Onshore Supply Chain
In addition to lower TCO and providing better support for your own production and customers, an onshore supply chain can deliver these key benefits:
1. Better Reaction Time
Anytime there’s a change in requirements, local suppliers can adjust faster because of reduced logistics/shipping time. Reaction time is also important right now because as demand changes, a domestic supplier can scale up or down more quickly.
2. Lower Lead Times & Speed To Market
Manufacturers are constantly requiring lower lead times and a domestic supply chain can meet those demands thanks to fewer logistics and shipping issues. Domestic partners are more agile to respond when transportation from the manufacturing site to point of use only includes roads.
3. Less vulnerability to Global Events
Domestic manufacturing partners offer greater stability when disruptive events happen overseas. Here, in the U.S. we have more stability when it comes to raw materials, energy pricing, and other disruptive circumstances. Facts and news also are easier to obtain, when domestic disruptions occur too.
4. High Quality Due to Higher Transparency
Sourcing parts domestically means you can stop by a factory and see your parts on the line. You’ll have more control by being able to visit the supplier and ensure that their quality and processes meet requirements – versus when you’re making assumptions through an audit process with an overseas supplier.
5. Value Engineering Support
Working with a local partner can mean that you get help at the front-end of your project, which can reduce TCO. In my experience, when you can sit face-to-face and walk through a design application and engineer costs out–that’s a huge advantage. There is also an advantage at the engineering stage in that there is no language barrier or technical misunderstandings with a domestic supply chain partner.
Steps To Re-Shoring Your Supply Chain
Re-shoring is a huge initiative. I guide our customers to follow these few first steps:
Step 1
First, look at your supply chain strategy and determine how much risk is associated with it. Take a high-level view and then look at certain parts in particular that are higher risk and start with that one part. Supplier by supplier and part by part will speed it up a little bit.
Step 2
Next, start defining which parts would fit the domestic supply base. Moving specific parts first is a manageable way to begin re-shoring.
Step 3
This is a critical step – start digging into TCO of sourcing products overseas and try to uncover your hidden costs on the offshore side.
Step 4
Get strategic help from a trusted supply chain partner who has experience supporting customers with re-shoring initiatives.
While there is a bit of an investment in time and money to bring your supply chain onshore, it’s an investment to ensure peace of mind that you ‘re able to get the parts when you need them.
We’re always ready to support our customers with solutions to improve the stability and security of their supply chains through fastener sourcing, world-class manufacturing, engineering services, customized VMI programs, and much more. Contact us for help.