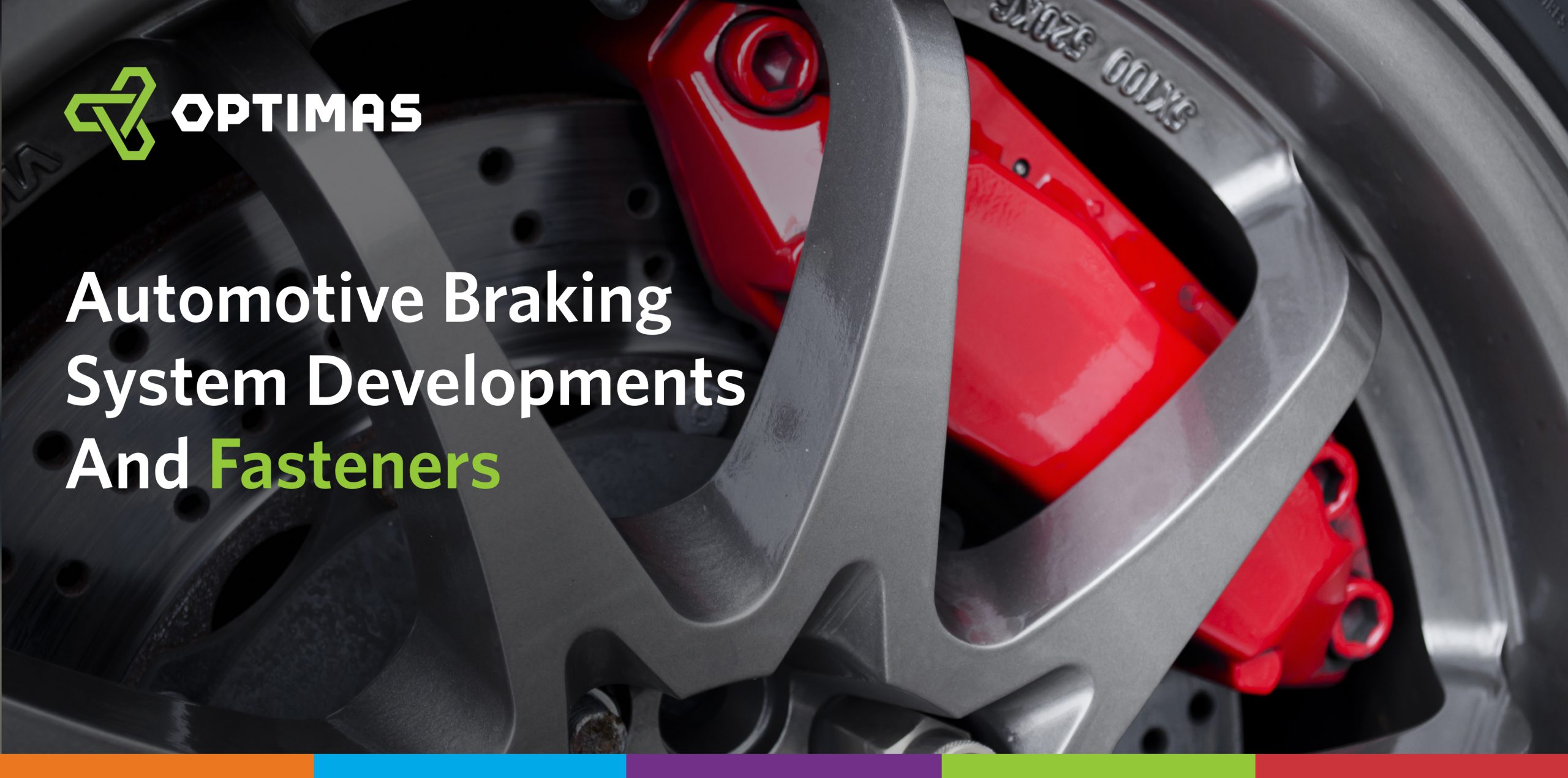
Automotive Braking System Developments & Fasteners
Automotive braking systems is an example of technology that has seen little change over the years gone by, however big developments are on the horizon for the market. Here’s an update on what to expect in the industry surrounding the automotive braking system, as well as the importance of the fasteners used in these systems.
Rise in Vehicle Safety Features
Vehicle safety features are a driver for growth of the automotive braking system market, which is currently valued at $29.86 billion as of this year and predicted to register a CAGR (compound annual growth rate) of 3.64% between now and 2028.
Manufacturers are already producing systems that integrate anti-lock braking systems (ABS) with electronic stability control (ESC) to be compatible with autonomous emergency braking systems which sense the chances of the vehicles collision and automatically brakes to mitigate it.
In order for these developing safety features to work effectively, high-strength and durable fasteners are essential. Here is a list of fasteners used within automotive brake systems:
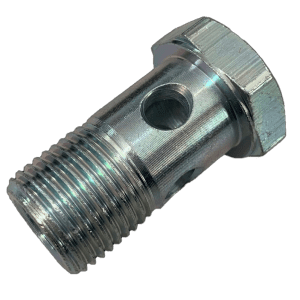
Automotive Braking System: Banjo Bolt
- Banjo Bolts – connects the brake hose fitting to the calliper inlet
- Solenoid Valve Component – A built in ABS / ESC hydraulic block which applies or removes hydraulic pressure on command from the electronic control unit (ECU)
- Hose Fittings – Connect the master cylinder to the brake calliper for the transfer of pressurised brake fluid
- Guide Rod & Guide Pin – Rods guide the proper connection between the brake calliper and the calliper bracket, and then pins guide the proper connection angle between the brake pad and rotor
- EPB Nut & Screw Assembly – Functions as an actuator component of the electric parking brake as well as transferring torque to the piston
For the automotive braking system to function properly, it is essential the components are fastened together with reliable, durable fasteners.
At Optimas, we can source all your automotive braking system fasteners through our 4,000 global supplier network and leveraged purchasing power.
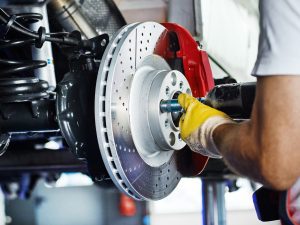
Installation of Disc Brake with Calliper
Regenerative Braking System Growth
Alongside the rise of safety features boosting the automotive braking system market, sustainable braking systems are becoming increasingly sought after due to Government initiatives to reduce emissions. In 2022, the British Government granted nearly £200 million to areas of the UK for its Zero Emission Bus Regional Areas (ZEBRA) scheme to fund 943 battery-electric and hydrogen buses.
Regenerative braking systems capture a vehicles kinetic energy and uses it to recharge the batteries. Due to the high-mile range on buses, regenerative braking systems are seen as a great component to use for these vehicles and their demand has clearly grown after the regenerative braking system market was estimated to have seen year over year growth at 45.10% in 2021. Therefore, this type of braking system will help boost the growth of electric and hybrid vehicles, thus creating more of a demand for suitable fasteners in these vehicles.
However, alongside the energy recovery system for electric vehicles such as regenerative braking, there are also mechanical energy recovery systems. By converting kinetic energy of the wheels and driveshaft into stored mechanical energy, it is released back to the driveshaft for acceleration – this is usually found within the flywheel system that supports braking of the vehicle and helps store energy. It is essential that these key systems are fastened together with high-strength, durable parts.
With over 90 years’ experience cold-forging fasteners, Barton Cold-Form, Optimas’ UK manufacturing division in Droitwich, their cold-formed fasteners are ideal for electric vehicle applications.
Barton has the capability to produce automotive braking system fasteners in a wide range of lightweight materials to contribute to improved vehicle acceleration and fuel efficiency. Furthermore, cold-forming maximises a part’s metallurgical properties, prioritising strength, and durability by ensuring its structural integrity, offering an advantage over traditional, machined parts; these high-strength fasteners are crucial for automotive braking systems.
Brake-by-Wire Developments
Continuing on from further automotive braking systems, as the brake-by-wire system has seen developments. A brake-by-wire system controls the brakes of a vehicle through the use of electricity, which differs to a traditional hydraulic system and removes the mechanical connection between the user and the vehicle.
The system works by controlling the brakes using electricity and uses a sensor to monitor the force a driver uses on the brake pedal. The vehicles ECU then relays a message to the electric pump to produce the desired amount of pressure required to slow down or stop the vehicle.
Current brake-by-wire systems still use hydraulics despite the electric pump generating the pressure to apply the brakes, however the end goal for testing of the system will be to make it solely electronically controlled and actuated.
As seen across the automotive industry, different systems are moving towards electric. Therefore, the fasteners manufacturers use in their builds need to be suitable for these systems. Electric vehicles tend to be much heavier than their petrol or diesel counterparts due to their batteries, so using lightweight materials at every opportunity is crucial to lessen emission and heighten vehicle performance. Even down to fasteners, it’s important you prioritise using light-weight materials at every opportunity to optimise battery performance.
Revolutionary AI Braking
There are certainly changes to the automotive braking system regarding electricity, however Brembo (Italian brake-maker) plan to take the system to the next level through artificial intelligence.
Using a new system, Sensify, enables precise vehicle control by constantly applying different brake force to each of the four wheels independently, rather than per axle. Actuators on each wheel are triggered by the ECU that constantly monitors parameters such as road surface friction, vehicle mass, weight distribution, speed etc… which all affect brake performance.
Alongside the system providing a greater degree of control for the driver under both normal and panic situations, it also controls the position of the brake pads which can minimize drag between pads and discs, resulting in improved fuel consumption for the vehicle.
Production is set to roll out in 2025, therefore manufacturers will need to establish how they can integrate these new systems into their automotive builds, to ensure they have the most suitable components necessary.
Optimas Can Support You
Through Optimas’ global supplier network, we can help you source or design the right fastener for your automotive braking systems. Our engineers have the expertise and technology to address your unique design requirements and assembly needs, from secondary operations to exotic materials.
The smallest fasteners and components can have the biggest impact on your business. That’s why we focus on finding solutions that improve efficiency and drive profitable growth across your enterprise. Get in touch with us today so we can help and provide solutions to enhance your efficiency.