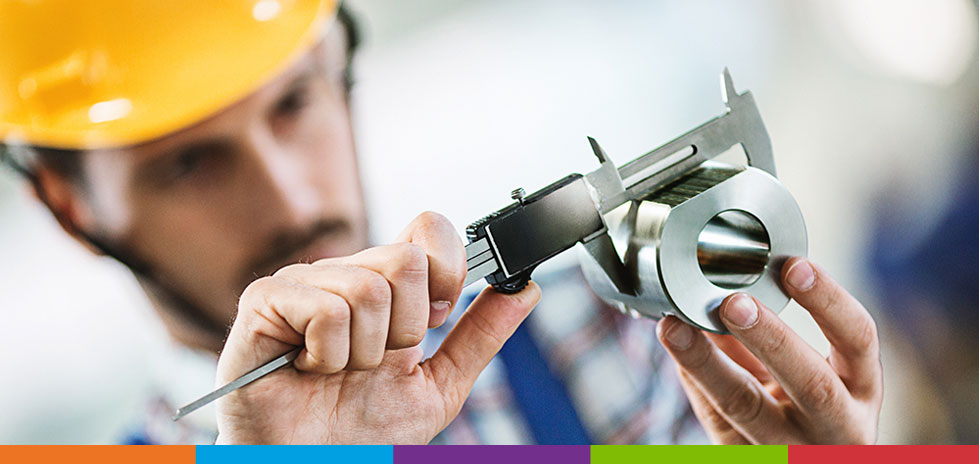
Automated Inspection Technology: Your Options for Improving Process Efficiency
Quality assurance has long been a priority for manufacturers, ensuring that substandard products never leave the floor. However, large production runs allow for some human error during the inspection process, leading to waste, recalls, and other costly issues.
Adding automated inspection technology to your operations can keep those disruptions at bay, improving accuracy and boosting the overall efficiency and consistency of your inspection process.
3 Types of Automated Inspection Technology
Currently, three types of inspection tech dominate the manufacturing automation space:
Attribute inspection:
This approach employs optical or mechanical means to determine whether a particular attribute conforms to a given requirement without human intervention. Optical attribute inspection involves taking a picture of a part and comparing its silhouette to that of an acceptable or unacceptable image. At a pace of one to two inspections per second, automated optical inspection improves process efficiency and yields an average defect rate of less than 50 parts per million.
Dimensional inspection:
Here, an array of lasers measures the characteristics of each dimension of a part. Similar to optical attribute inspection, this process begins with a comparison based on a predetermined gauge of acceptability. Dimensional inspection can only inspect what sensors can “see,” meaning it cannot measure internal or recessed features. However, due to its 360-degree measurements, a dimensional quality inspection provides very accurate results — though at a slower rate of roughly 30 seconds per part.
Coordinate-measuring machines:
These use “touch,” either with mechanics or laser probe, to inspect a part. The slowest method of automation inspection technology, coordinate-measuring machines need several minutes to assess complex parts, but they can measure internal features and compare them to specifications with greater accuracy.
Automation inspection technology can provide levels of accuracy previously only possible via sophisticated analog laboratory instruments. It’ll become much easier to define specifications, handle materials, respond to changes, and adapt the line for greater process efficiency. But as bright as this future may be, the selection process is critical to finding the right solution.
Understanding Automated Inspection Options
Before implementing automation inspection technology, it’s critical to ensure the solution is suited for your operations and will provide the intended results. Make sure to ask:
Is the solution as thorough as you need it to be?
Remember that not every piece of automation inspection technology can see the whole part. As already mentioned, a dimensional inspection cannot measure the acceptability of interior features, so coordinate-measuring machines may be more appropriate for your operations. Understand, however, that irregular and asymmetrical features may pose some difficulties and may need to be compensated for with different software.
Can it measure functional characteristics?
Automated gauging does have limitations when it comes to measuring functional characteristics (i.e., what determines whether the part will operate as intended). This means you may need mechanical gauges that emulate the functional environment to validate automated inspection technology findings. Following this, the automated inspection equipment can measure overly complex features and characteristics.
Again, it’s all about finding the right solution for your operations to guarantee accuracy while bringing about greater process efficiency and cost reductions. Otherwise, you won’t enjoy all the advantages manufacturing automation can offer to quality assurance.