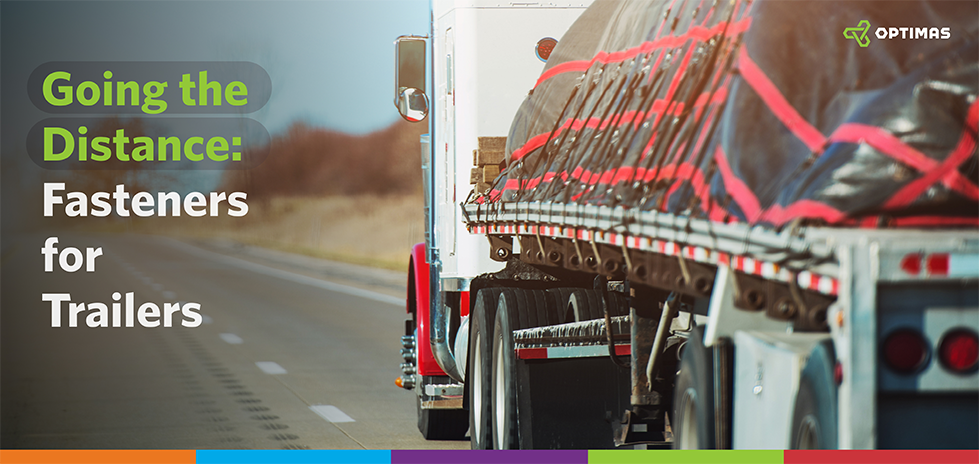
Going the Distance: Fasteners for Trailers
With over 600,000 HGVs on UK roads last year, the number of trailers in daily use is prolific. However, with supply chain uncertainty still looming on the horizon, and an increasing number of governments clamping down on Co2 emissions, trailer manufacturers are under pressure to reimagine the production and design of their builds.
However, these incoming environmental regulations bring with them a chance for a fresh perspective on trailer manufacturing. From the beginning of 2024, the EU will begin certifying trailers according to their CO2 emissions, encouraging a number of European manufacturers to revolutionise their engineering principles to create new types of eco-friendly powertrains and braking systems. A plethora of manufacturers are opening manufacturing plants in the UK, to better meet demand for semi-trailers in the country.
As is the case with many industries, trailer manufacturers are expected to meet demand in the face of exciting new alternative fuel prospects and an ever-growing requirement for HGV transportation. Although the situation is decidedly better than in 2020, geopolitical conflicts have once again reduced supply chains to a state of flux. Maintaining a steady and reliable supply of quality parts is crucial for manufacturers looking to meet demand and boost their product output.
The Importance of Quality Parts
Trailers require a number of standard and specialised parts. In the face of supply chain instability, manufacturers must prioritise using quality fasteners in the initial design stage of a build, to avoid last-minute, costly purchase orders and delayed time to market.
Fasteners can make up less than 1% of the cost of a production build, but they can constitute more than 50% of a product’s parts. Plus, these parts may be small, but they can have a significant impact on vehicle performance, affecting speed, fuel consumption, range and overall performance.
This is particularly the case for trailers. Making up a significant portion of a build’s BOM, these parts are included in a trailer’s sub-frames, floor and storage compartments, vent openings, skin reinforcements, firewall assembly and load-weight systems. Some standard fasteners for trailers can include:
- Wheel nuts
- Stud connectors
- Wheel bolts
- Cable ties
- Flange Bolts
- Bolt washers
- Sealing washers
- Lockbolts
- SEMs
Travelling long distances with heavy loads, and often in extreme temperatures, fasteners for trailers need to be:
- Vibration resistant
- Corrosion resistant, to withstand acid washing
- Lightweight
- Require minimal maintenance
- Maintain very high tensile and fatigue strength
To satisfy this list of requirements, the material of a fastener needs to be carefully considered. Fasteners for trailers are often made from steel or stainless steel, and coated with zinc, or zinc flake. Electric or hydrogen trailers, alongside others powered by alternative fuels, may demand more specialised fasteners made of aluminium and titanium to prioritise lightweighting.
Maintaining a Streamlined Supply
While manufacturing trailers using quality parts is key, to get these parts to a production line it’s crucial manufacturers maintain a streamlined supply chain.
A supply chain relies significantly on HGVs for the transportation of goods, but the demand for manufacturing HGVs and trailers is increasing, as businesses struggle to source the parts to produce them.
The past couple of years have highlighted the importance of onshoring and nearshoring, as evidenced by the number of manufacturers opening up new plants nearer their customer base. Not only does onshoring ensure a steady and reliable stream of parts, but it also lowers manufacturers’ carbon footprints, as fasteners require minimal transportation.
With fastener distribution centres all over the globe and cold-form manufacturing facilities on both sides of the Atlantic, we’ve partnered with manufacturers for over 100 years helping them to meet demand by sourcing quality parts, closer to home.
Alongside our offering of both standard and specialised fastening solutions, our OptiTech VMI solutions ensure our partners receive their parts on time, every time, using advanced cloud-based technology. With manufacturing, distribution and engineering all under one roof, we can help you streamline your supply chain and optimise your product quality.