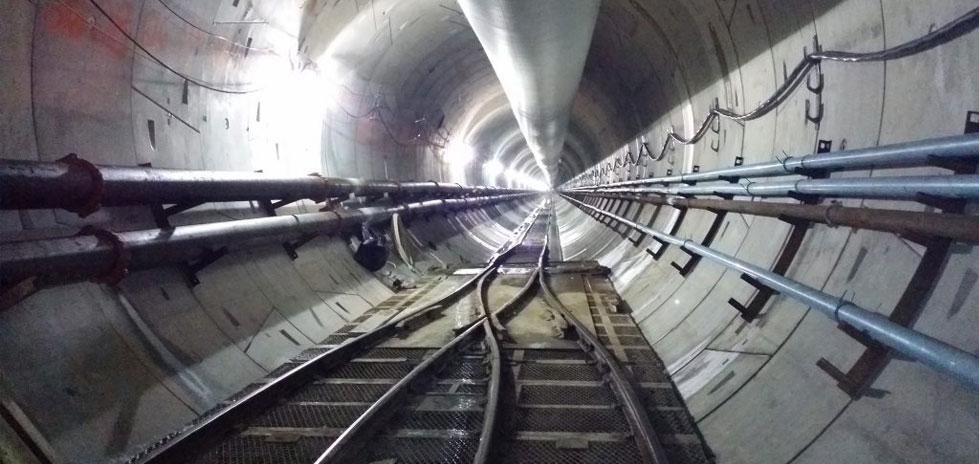
Ihr Tunnel ist nicht wie jeder andere: Warum sollten Sie Ihre Komponenten reparieren?
Tunnel gehören zu den schwierigsten und komplexesten Tiefbauprojekten. Daher sind auch die standardmäßigen Verbindungs- und Richtsysteme, die zum Verbinden der Tunnelabschnitte erforderlich sind, hochtechnisiert. Einige Tunnelprojekte stellen jedoch einzigartige Herausforderungen dar, denen Standardteile nicht gewachsen sind. Die Tunnelabteilung von Optimas Solutions weiß, dass die Überarbeitung bestehender Lösungen zur Erfüllung bestimmter Anforderungen oder die Entwicklung brandneuer Produkte einen großen Beitrag zur Verbesserung der Tunnelbauaktivitäten und des Endergebnisses leisten können.
Sandrine Ordener, Engineering Director der Tunnel Division von Optimas Solutions, erklärt, wie Ihr Projekt von technischen Tunnelbefestigungslösungen profitieren kann.
Wie wir in einem früheren Artikel besprochen haben, gibt es kein Standard-Tunneldesign. Jedes Projekt stellt neue Herausforderungen dar, basierend auf Endzielen, Budget, geografischer Lage, Bodenverhältnissen, lokalen Praktiken und Sicherheitsanforderungen. Daher müssen Tunnelauskleidungen diesen Bedingungen entsprechen, um Tübbinge und Ringe angemessen zu verbinden. Das bedeutet, dass standardisierte Befestigungslösungen nicht immer den spezifischen Herausforderungen und Bedürfnissen eines Tunnelprojekts gerecht werden.
Befestigungskomponenten werden verwendet, um separate Tunnelringe und -segmente zu verbinden, was dazu beiträgt, die Festigkeit der gesamten Konstruktion zu unterstützen. Daher sollten Befestigungslösungen dazu beitragen, den Tunnel gegen das Eindringen von Wasser abzudichten und ein Öffnen der Tunnelringe oder eine Ovalisierung des Tunnels zu verhindern.
Eine Reihe von Aspekten kann diese Installationsaufgaben noch schwieriger machen. Einige der Faktoren, die eine wichtige Rolle spielen können, sind lokale Bedingungen wie korrosive Umgebungen oder die Wahrscheinlichkeit seismischer Ereignisse.
In solchen Fällen können ansonsten zuverlässige Standard-Tunnelbefestigungslösungen anfällig für frühzeitige Ausfälle sein, die anschließend die Lebensdauer des gesamten Tunnels beeinträchtigen. Zum Beispiel sind Standardsteckverbinder möglicherweise nicht in der Lage, Korrosion zu widerstehen, Stärke und Flexibilität bei Erdbeben auszugleichen oder hohen Belastungen standzuhalten.
Im Gegensatz dazu werden maßgeschneiderte Befestigungskomponenten konzipiert, um den individuellen Bedürfnissen und Herausforderungen eines Tunnelprojekts gerecht zu werden, und werden daher einen höheren Standard erfüllen. Darüber hinaus können schlüsselfertige Lösungen die Verbindung von Ringen und Segmenten vereinfachen und beschleunigen und so die Produktivität vor Ort verbessern. Um Tunnelbefestigungskomponenten kundenspezifisch anzupassen, folgen erfahrene Spezialisten wie die Tunnelabteilung von Optimas einer strengen Methode, die die zeit- und kosteneffiziente Lieferung hochwertiger, geeigneter Teile gewährleistet.
Der Prozess hinter maßgeschneiderten Tunnelbefestigungsdiensten
Der Prozess zur Optimierung oder Innovation einer Tunnelbefestigungskomponente beginnt mit einer Kundenanfrage. In dieser Phase sind Kommunikation und Feedback der Schlüssel zum Verständnis der einzigartigen Bedürfnisse eines Projekts. Ein erfahrener Hersteller von Tunnelbefestigungslösungen wird diese ersten Gespräche nutzen, um festzustellen, ob ein Standardbauteil passt oder ob eine kundenspezifische Lösung erforderlich ist. Außerdem kann der Spezialist dann feststellen, ob eine einfache Neukonstruktion oder Optimierung eines bestehenden Bauteils ausreicht oder ob innovative, fabrikneue Teile erforderlich sind.
Um beispielsweise die Herausforderungen des Tunnelbaus in korrosiven Umgebungen wie im Projekt der Inner Doha Resewage Implementation Strategy (IDRIS) in Katar anzugehen, nutzte die Tunnel Division von Optimas ihr Fachwissen, um ein Standard-Injektionssystem neu zu entwerfen, das hochdichtes Polyethylen (HDPE) aufnehmen kann ) Inliner und erhöhen die Widerstandsfähigkeit sowie die Lebensdauer der Auskleidung.
Basierend auf der ersten Bewertung und den vereinbarten Projektspezifikationen ist die nächste Stufe des Innovationsprozesses die Erstellung eines Designkonzepts für das kundenspezifische Bauteil. In dieser Phase werden Materialien, Formen und zusätzliche Features definiert. Anschließend testen Ingenieurteams die Gültigkeit des ursprünglichen Entwurfs durch virtuelle Simulationen (In-Silico-Tests), z. B. Finite-Elemente-Analyse.
Hat sich das theoretische Modell bewährt, werden mit 3D-Druck oder anderen Rapid-Prototyping-Verfahren erste Proofs of Concept und Prototypen erstellt. Diese werden dann verwendet, um Labor- und Praxistests durchzuführen, um die Eigenschaften des Bauteils zu bewerten und seine Fähigkeit zu beweisen, die anfänglichen Kundenanforderungen zu erfüllen.
Es überrascht nicht, dass die Testprotokolle nicht standardisiert sind, da die Testanforderungen je nach den in den ersten Planungsphasen festgelegten Projektspezifikationen stark variieren. Daher sollte der Hersteller eng mit dem Kunden zusammenarbeiten, um zu definieren, welche Tests erforderlich sind. Um die Lieferung einer qualitativ hochwertigen Lösung zu gewährleisten, können bestimmte Qualitätsstandards angewendet werden, auch wenn keine Zertifizierung erforderlich ist.
Beispielsweise halten sich die spezialisierten Teams der Tunnel Division von Optimas an die Qualitätsstandards von ISO 9001. Außerdem hat das Unternehmen für seine Sofrasar-Produkte ein eigenes Qualitätskontroll- und Qualitätssicherungssystem (QCQA) definiert. Das QCQA-System überwacht die gesamten Herstellungs- und Lieferkettenprozesse, von der Rohstoffbeschaffung bis zur Auslieferung an den Kunden. Im QCQA-Rahmen von Optimas umfasst jeder Vertrag umfangreiche Dokumentationen wie technische Datenblätter, Listen früherer Projekte, Lieferzertifikate und Packlisten.
Basierend auf den erhaltenen Ergebnissen kann das Bauteildesign oder das Herstellungsverfahren weiter optimiert werden, um die Produktleistung oder die Wiederholbarkeit und Reproduzierbarkeit des Herstellungsprozesses zu verbessern. Sobald das endgültige, optimale Bauteildesign erreicht ist, erstellt der Hersteller eine neue, eindeutige Teilenummer, die das Bauteil identifiziert, und fährt mit der Herstellung und Lieferung der ersten Chargen fort.
Qualifizierte Experten für Tunnelkomponenten können in kurzer Zeit hochwertige kundenspezifische Komponenten liefern, um einen agilen Tunnelbau zu ermöglichen. Im Allgemeinen kann der gesamte Entwicklungsprozess innerhalb von ein bis zwei Monaten abgeschlossen werden, um bestehende Komponenten zu modifizieren, oder in acht bis 24 Monaten, um innovative Lösungen zu entwickeln, wenn mehr Tests erforderlich sind.
Die unterschiedlichen Phasen der Realisierung maßgeschneiderter Komponenten erfordern unterschiedliche Fähigkeiten und Kompetenzen. Dies bedeutet oft, dass Kunden verschiedene Parteien kontaktieren müssen, um Beratungen zu Komponentenspezifikationen, Design, Prototyping, Tests und Herstellung des Endprodukts zu erhalten. Spezialisierte Unternehmen wie die Tunnel Division von Optimas können für all diese Aktivitäten einen einzigen Ansprechpartner bieten.
Unter Bezugnahme auf das obige Beispiel war Optimas' Tunnel Division dank ihrer hauseigenen Konstruktions- und Fertigungskapazitäten in der Lage, das korrosionsbeständige Injektionssystem zu produzieren und zu liefern, das für das Tunnelprojekt in Doha, Katar, benötigt wurde.
Erfahrene Tunnelbefestigungsspezialisten können auftretende Herausforderungen angehen
Ob die Optimierung eines bestehenden Bauteils oder die Entwicklung eines neuen, beide Verfahren stellen Herausforderungen dar. Es ist die Aufgabe des Konstrukteurs, diese Herausforderungen zu meistern und ein qualitativ hochwertiges Teil zu liefern, das deutliche Leistungsverbesserungen aufweist und gleichzeitig für den Einsatz in einem kommerziellen Projekt wirtschaftlich rentabel bleibt.
Die Bewältigung der Herausforderungen und das Finden des Gleichgewichts können durch Befestigungsspezialisten mit einem tiefen Verständnis der Tunnelindustrie, fortgeschrittener Produktkompetenz und Material- und Technologiekenntnissen für eine kontinuierliche Entwicklung erreicht werden.
Nach Abschluss von über 400 Projekten umfasst das Sofrasar-Sortiment nun mehr als 500 Standardprodukte – jedes ursprünglich für eine bestimmte Anwendung entwickelt. Optimas Sofrasar ist proaktiv und verpflichtet, seine Kunden durch die Verbesserung von Standardkomponenten zu unterstützen oder neue Lösungen zu entwickeln, die den individuellen Anforderungen von Tunnelprojekten entsprechen. Das Unternehmen verfügt über mehr als 20 Jahre Erfahrung in der Branche und kann daher die projektspezifischen Anforderungen für jeden Tunnelbau leicht verstehen und ansprechen. Dank der hauseigenen Konstruktions-, Fertigungs- und Qualitätsprüfeinrichtungen sind wir in der Lage, hochwertige, langlebige Befestigungslösungen anzubieten, die dem Tunnelsegment große Vorteile bringen können, indem sie die Montage vereinfachen und beschleunigen und gleichzeitig die Gesamtleistung verbessern.
Mehr darüber lernen Tunnelabteilung.