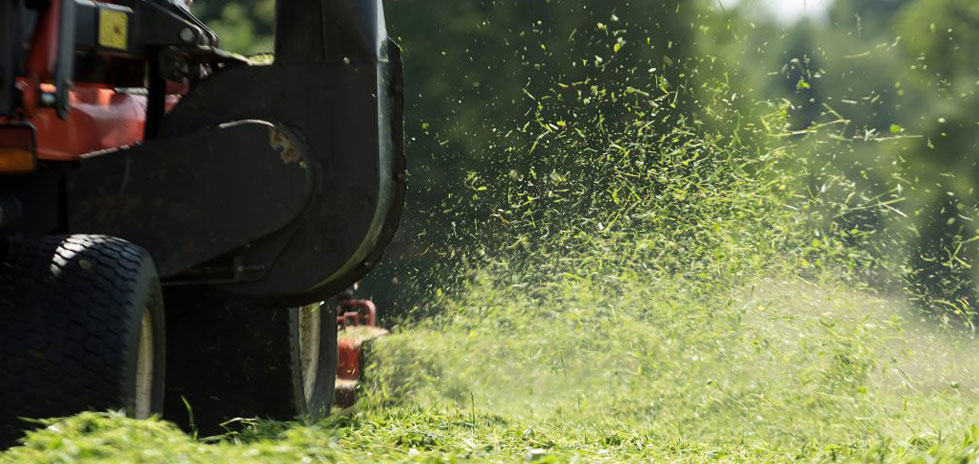
Eine Schraube bietet dem Hersteller von Aufsitzmähern mehrere Vorteile
Die Einführung eines neuen Modells kann Herstellern eine Chance bieten. Eine Gelegenheit, die Produktionsmethodik weiter zu optimieren und neue technische Lösungen auf den Markt zu bringen. Dies ist genau die Gelegenheit, die ein führender US-Anbieter von Outdoor-Power-Equipment nutzte, um seinen neuen Aufsitzmäher zu unterstützen. Mit Hilfe eines externen Lieferantenpartners, Optimas Solutions, war der Hersteller in der Lage, gleichzeitig die Komponenteninvestitionen zu reduzieren und dennoch eine hochentwickelte Lösung für die Anwendung zu liefern.
Dieser Hersteller ist eine tragende Säule im Rasen- und Gartensektor und bietet seit über 50 Jahren marktführende Elektrowerkzeuge für den Außenbereich. Im Laufe der Jahre hat das Unternehmen ständig daran gearbeitet, seine Designs zu optimieren, um mit den Bedürfnissen seiner Kunden Schritt zu halten. Als sich die Chance bot, ein Verbindungselement von Grund auf neu zu gestalten, ergriff das Unternehmen die Gelegenheit mit beiden Händen.
Letztendlich wollte der Hersteller bei seinen neuen Aufsitzmähermodellen auf Komponenten aus hochfestem/niedriglegiertem Stahl (HLSA) umsteigen. Dies würde bessere mechanische Eigenschaften bieten. Darüber hinaus zielte das Unternehmen darauf ab, auf der neuen Plattform Schrauben mit kleinerem Durchmesser anstelle der derzeit verwendeten Komponenten mit 5/16-Zoll-Durchmesser zu verwenden, was die Stückliste (BoM) vereinfachen und somit einen Mehrwert für die Lieferkette schaffen würde. Die Einführung der Schrauben würde auch dazu dienen, die Zuverlässigkeit zugehöriger Gelenke an dem Aufsitzmäher zu verbessern, was Garantieverbesserungen ermöglichen würde.
Der Hersteller holte die Hilfe des Befestigungsexperten Optimas in Anspruch, um bei der Konstruktionsspezifikation zu helfen, ein Prozess, an den sich Mike Eusanio, Anwendungsingenieur bei Optimas, gut erinnert: „Entwicklung einer Schraube, die ein verbessertes Verhältnis von Antrieb zu Abisolierung in der neuen, dünneren Schraube bietet Stahlmaterialien, die der Kunde gewählt hatte, war wichtig. Sie wollten auch die Gesamtzahl der Gelenke in der Plattform im Vergleich zu früheren Aufsitzmäher-Designs reduzieren. Dies würde direkt mit einer Effizienzsteigerung korrelieren. Durch die Entwicklung einer idealen Schraube mit einer optimal gestalteten Gegenmutter konnten wir dem Kunden helfen, diese Ziele zu erreichen.“
In Zusammenarbeit der beiden Designteams wurde nachgeforscht, um die optimale Lösung zu definieren. Durch enge Kommunikation und ausgiebige Tests entschied sich der Hersteller für eine M6-Schraube, die die beste Leistung bot. Alle Arbeiten wurden termingerecht zum Entwicklungstermin des Aufsitzmähers des neuen Modells durchgeführt und das neue Bauteil erfolgreich in das Design integriert.
Eusanio führte die Testverfahren weiter aus: „Wir nutzten die bestehenden Einrichtungen an unserem Produktionsstandort für Verbindungselemente in Wood Dale, Illinois. An diesem Standort bieten wir unseren Kunden die Nutzung unserer hochmodernen Prüflabore an, mit denen wir die Eignung der von uns gelieferten Komponenten beurteilen. Wir haben umfangreiche Tests durchgeführt und Verbindungen mit vom Hersteller bereitgestellten Stahlplatten und Rahmenelementen simuliert. Durch diesen Ansatz konnten wir sicher sein, dem Kunden alle verfügbaren Ergebnisse zu liefern, um eine korrekte Entscheidung zu treffen. Mit Fertigungskapazitäten auch vor Ort konnten wir das Produkt schnell produzieren, obwohl das Gewindedesign exklusiv für diesen Kunden war.“
Die Einführung des neuen Verschlusses brachte zusätzliche Vorteile. In einem breiteren Programm zur Vereinfachung von Komponenten wird erwartet, dass das neue Befestigungselement eine bedeutende Rolle bei der Reduzierung der Befestigungselementanzahl um 30-40% bei zukünftigen Modellen spielt. Dies würde dem Hersteller helfen, die Gesamtkomponenteninvestition zu reduzieren und gleichzeitig die Herstellungszeiten zu verkürzen. Folglich stellte das neue Befestigungselement sofort einen Mehrwert für den Betrieb dar, wobei der Hersteller die Implementierung in seiner gesamten Produktpalette einführte, wo immer dies geeignet war.
Durch die Einführung neuer Komponenten in der Prototypenphase können Hersteller mit Hilfe eines Experten für Verbindungselemente greifbare Vorteile erzielen, die weit über das fertige Produkt hinausgehen und dazu beitragen, die Anwendungen von Verbindungselementen für das gesamte Unternehmen zu verbessern. Das neue Modell dient als Proof of Concept und stellt sicher, dass die weitere Implementierung wertschöpfend, zeitsparend bei maximaler Anwendungstauglichkeit erfolgen kann. Dies sind die Arten von Vorteilen, die für einen OEM-Hersteller schwer zu ignorieren sind.