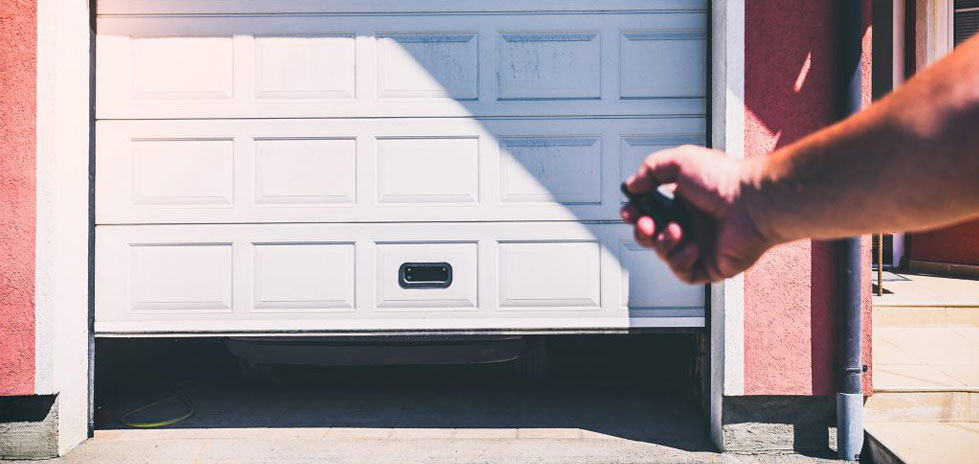
Engineered Fasteners reduziert Ausgaben für Komponenten um 75% für Hersteller von automatischen Türen
In einer wettbewerbsorientierten globalen Wirtschaft ist es wichtig, Effizienz in allen Phasen der Produktion zu finden. Viele Hersteller versuchen, den Stress in der Lieferkette durch verbesserte Logistikstrategien zu verringern, aber das ist nicht der einzige Bereich, in dem Verbesserungen möglich sind?
Es ist möglich, Stress aus der Lieferkette zu entfernen, indem die Komplexität der bestellten physischen Komponenten in Frage gestellt wird. Durch die Vereinfachung der in einem Produkt verwendeten Befestigungselemente ist auch die Beschaffung von Hardware einfacher. Als globaler Distributor und Engineering-Dienstleister ist Optimas Solutions in der Lage, diese Lösungen zu identifizieren. Das Unternehmen hat diese Strategie kürzlich umgesetzt, um einen der führenden Hersteller von automatischen Zugangslösungen weltweit zu unterstützen.
Der Hersteller hat sich einen weltweiten Ruf für die Bereitstellung von automatischen Türöffnern, Fernbedienungen, Teilen und Zubehör aufgebaut. Langlebigkeit ist bei automatisierten Türen von größter Bedeutung, da sie über längere Zeiträume und bei starker Beanspruchung fehlerfrei funktionieren müssen, sodass das Unternehmen seine Konstruktionen häufig neu bewertet, um Verbesserungen zu ermitteln.
Die Geschichte beginnt während eines routinemäßigen Produktabrisses eines automatischen kommerziellen Sektionaltoröffners. Der Teardown wurde im Rahmen einer kontinuierlichen Verpflichtung zur Qualität durchgeführt, um alle Möglichkeiten zur Produktverbesserung innerhalb des bestehenden Designs zu identifizieren. Es wäre keine fruchtlose Übung. Der Fokus wandte sich bald der Bremsbaugruppe an der Türeinheit zu, die ein Federsystem enthielt, das aus vier geflanschten Messingbechern bestand, die Druckfedern an einem Bolzen mit Innengewinde hielten. Obwohl scheinbar harmlos, begannen die Ingenieurteams, das System zu untersuchen, was einige Entwicklungsmöglichkeiten aufzeigte.
Als erstes wurde die Wahl von Messing als Material für die vier Tassen untersucht. Obwohl es ideal für den Betrieb in Umgebungen ist, die potenziell Korrosionsrisiken bergen könnten, gab es keinen Grund, warum Messing in einer kommerziellen Sektionaltoranwendung enthalten sein sollte. Der Rest der Einheit bestand aus verzinktem Stahl, was die Wahl von Messing weiter ins Rampenlicht rückte. Außerdem wurden die Becher aus Messing geschraubt, was bedeutete, dass der Lieferant oft Schwierigkeiten hatte, die Produktionsanforderungen des Herstellers zu erfüllen. Dies belastete die Lieferkette, was die Produktionsverfügbarkeit gefährden könnte, wenn die Nachfrage nach dieser Komponente steigt.
Tim Day, Anwendungsingenieur bei Optimas, führt die nachfolgende Methodik aus: „Nach einiger Recherche fanden wir heraus, dass die Toleranzen, die durch die Bearbeitung des Bauteils gegeben sind, für diese Anwendung nicht entscheidend waren. Daher empfahlen wir einen kaltgeformten Ersatz aus kohlenstoffarmem Stahl von einem unserer kundenspezifischen Lieferanten mit einer galvanischen Zink- und klaren Chromatierung, die für den Korrosionsschutz während des Versands und der Teilehandhabung ausreichend wäre.“
Die Spezifizierung eines kaltgeformten Bauteils brachte eine Reihe von Vorteilen mit sich. Die Verwendung eines Multi-Die-Formers, der keine sekundäre Verarbeitung nach dem Formen erfordert, bedeutete eine erhöhte Produktionseffizienz. Die Kaltumformung reduzierte auch den Abfall und bot eine umweltfreundlichere Methode zur Herstellung der erforderlichen Komponente. Dies liegt daran, dass das Rohmaterial unter hohem Druck in die Matrize gepresst wird, wodurch kein Abfall entsteht. Die Herstellung konnte auch beginnen, ohne dass Konstruktionsänderungen an den Passkomponenten erforderlich waren, was während der Implementierung einen Mehrwert darstellte.
Tim fährt fort: „Durch die Auswahl einer Stahlalternative konnten wir die Kosten jeder einzelnen Komponente um 75% senken, was dem Hersteller von automatisierten Türen einen Mehrwert brachte. Ein vereinfachter Herstellungsprozess für die Komponente verringerte auch den bestehenden Druck innerhalb der Lieferkette, wodurch die Risiken, die die ursprüngliche Komponente für die Betriebszeit darstellte, direkt angegangen wurden. Infolgedessen konnten wir durch die Einführung einer einzigen Komponente einen Mehrwert liefern und die bestehende Lieferkette stärken.“
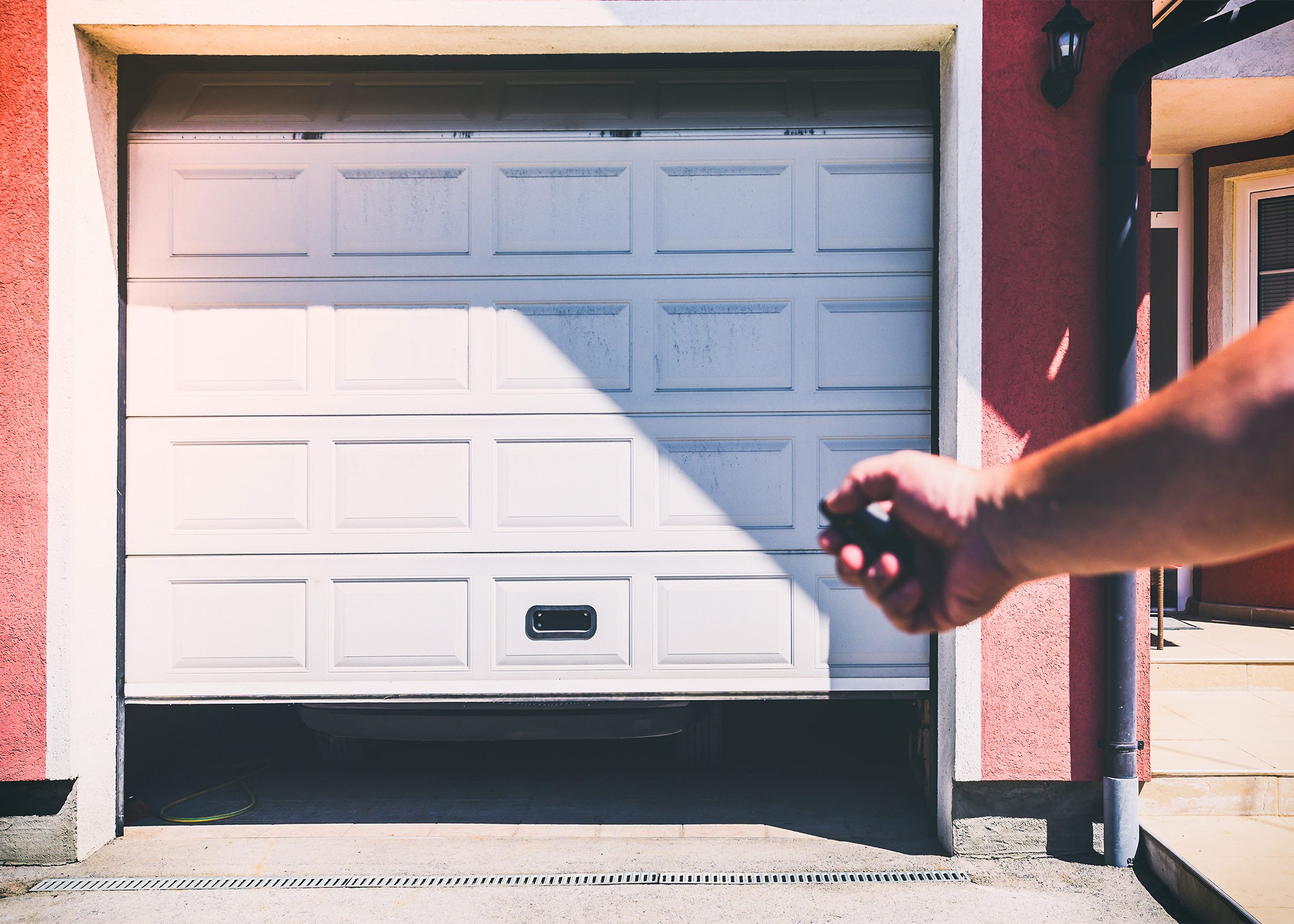
Garagentor PVC. Handfernbedienung zum Schließen und Öffnen des Garagentors.
Zufrieden mit der vorgeschlagenen Lösung führte der Hersteller die obligatorischen Lebenszyklustests durch, die alle seine Produkte durchlaufen müssen. Das Tor wurde über einen längeren Zeitraum kontinuierlich vorwärts und rückwärts betrieben. Dies ermöglichte es den Ingenieuren, alle Probleme in Bezug auf Ermüdung oder Korrosion während des Gebrauchs zu bewerten, alles wichtige Bedenken für ein Produkt, das in einer kommerziellen Anwendung stark genutzt wird. Nach erfolgreichem Abschluss der Tests wurde die Schale aus kohlenstoffarmem Stahl in dieses Modell des Sektionaltors integriert.
Abschließend sagt Tim: „Durch die Beauftragung von Optimas als externem Verbindungsexperten konnte der Hersteller eine Reihe von Lieferketten- und Anwendungsproblemen gleichzeitig angehen. Durch diesen integrierten Ansatz für Verbindungselemente kann es einfach sein, überspezifizierte Komponenten zu identifizieren, Alternativen zu finden und die gewählte Lösung mit sehr geringen Störungen des bestehenden Betriebs zu implementieren. Ich denke, jeder, der mit Großserienfertigung zu tun hat, kann den Vorteil darin erkennen.“