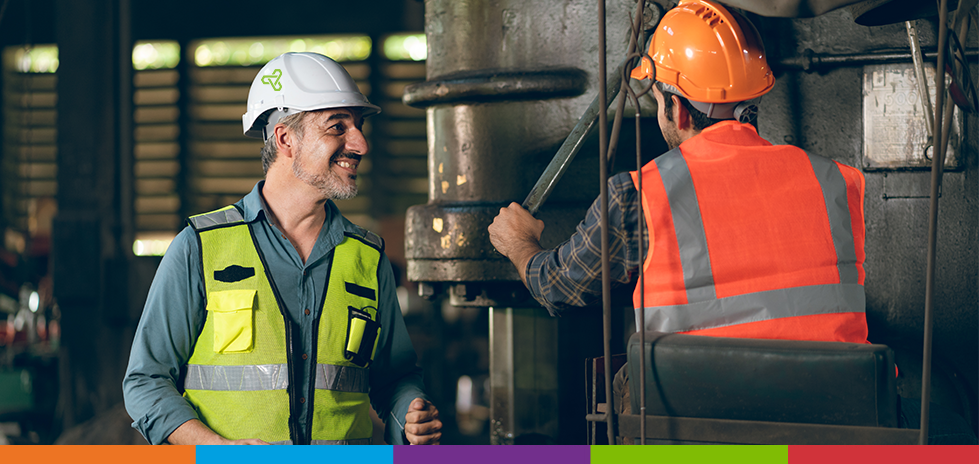
Entdecken Sie neue Produktionslinieneffizienzen mit einem Gemba Walk
Den Optimas Line Walk verstehen
Die durchschnittliche Zugehörigkeit zu unserem Engineering-Team beträgt 15-20 Jahre. Wenn also OEM-Betriebs- und Engineering-Experten Optimas-Experten wie Director of Engineering, Steve Adkins, oder Anwendungsingenieur, Mike Eusanio, zu einem Linienrundgang in ihre Einrichtung einladen, nicht, weil sie Probleme haben. Weil sie Lösungen wollen.
Ein Production Line Walk wird auch als a bezeichnet Gemba-Wanderung. Der japanische Begriff Gemba übersetzt „der eigentliche Ort“, der in der Fertigung die Werkstatt ist – der Ort, an dem die Fertigung abgeschlossen ist. Gemba-Kaizen ist ein Begriff, der verwendet wird, um das Konzept der kontinuierlichen Verbesserung zu beschreiben, das darauf abzielt, Prozesse zu verbessern und Verschwendung zu reduzieren.
Ein Line Walk bringt Unternehmensleiter aus Einkauf, Betrieb und Technik zusammen, um mit eigenen Augen zu sehen, wie sich Teile durch die Produktion bewegen. Die Erfahrung zeigt oft Lücken zwischen der Gestaltung von Prozessen und ihrer Durchführung. Ziel ist es, potenzielle Produktivitäts- und Effizienzsteigerungen zu identifizieren und gleichzeitig logistische Herausforderungen anzugehen.
Was erwartet Sie bei einem Line Walk?
Die kurze Antwort ist Fragen. Sie können davon ausgehen, dass unsere Experten ihnen viele Fragen stellen werden, da wir eine besondere Perspektive in der Anwendungsentwicklung, Installation und Fertigungstechnik in die Verwendung von Verbindungselementen einbringen. Bei Bedarf ziehen wir sogar unsere eigenen Lieferanten hinzu, um einen umfassenden Überblick über alles, was wir liefern können, zu teilen.
Gespräche beginnen in der Regel mit Personen vor Ort. Wir binden Bediener so weit wie möglich ein, damit wir verstehen, was sie sehen, und ihre Herausforderungen dokumentieren. Lösungen werden gemeinsam mit den betroffenen Menschen entwickelt.
Vor Beginn des Walks oder in den ersten Zellen oder Phasen einer Produktionslinie suchen wir nach Prozessverbesserungen, indem wir Produktionsleitern Fragen stellen wie:
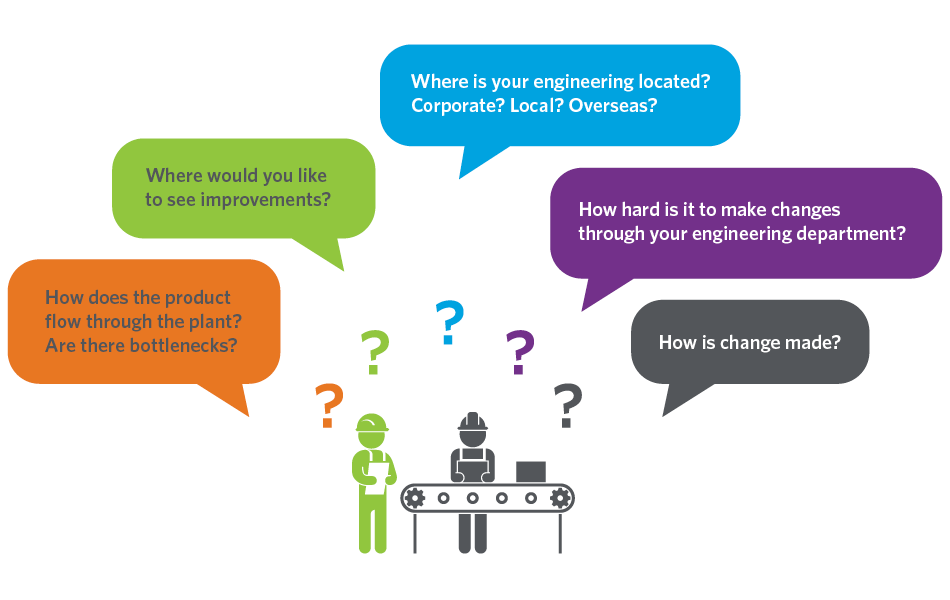
Wo würden Sie sich Verbesserungen wünschen?
- Was sind Ihre Reduzierungsziele (Teile, Zeit, Geld)?
- Wie viele Teile möchten Sie konsolidieren oder eliminieren?
- Suchen Sie nach Durchsatzverbesserungen?
- Gibt es Qualitätsprobleme zu lösen?
- Haben Sie Probleme mit der Liefereffizienz, Teile schnell an den richtigen Verwendungsort zu bringen?
- Haben Sie Designprobleme erlebt?
- Sind hier Installationsprobleme zu beheben?
Wie fließt das Produkt durch die Anlage?
- Sind die Engpässe?
Wo befindet sich Ihre Technik?
- Unternehmen? Lokal? Übersee?
Wie schwierig ist es, Änderungen durch Ihre Konstruktionsabteilung vorzunehmen?
Wie wird verändert?
- Wie können wir Verbesserungen mit Blick auf die Einfachheit vornehmen, sodass Änderungen unkompliziert und schnell zu implementieren sind und nicht viele neue Tests erfordern?
Letztendlich führen wir einen Line Walk durch, um die Umgebung zu verstehen, in der wir Verbindungselemente liefern und/oder den Bestand verwalten, und um die Leistung unserer Teile sicherzustellen.
Jeder Line Walk endet mit einer mündlichen Zusammenfassung unserer Beobachtungen und empfohlenen Maßnahmen, gefolgt von einer E-Mail-Zusammenfassung von allem, was vor Ort besprochen wurde.
Einige Empfehlungen können zu etwas höheren Kosten pro Stück führen. Sie jedoch immer niedrigere Gesamtbetriebskosten und/oder machen es einem Bediener einfacher/schneller, eine Aktivität abzuschließen.
Vorteile eines Line Walk/Antworten
Da die Hersteller in der Regel Verbindungsexperten im Haus haben, bleiben mehrere Möglichkeiten zur Effizienzsteigerung unbemerkt.
Beispielsweise können Sie mehrere Lieferanten von Verbindungselementen haben, die Teile an einer Anlegestelle abliefern. Jemand muss jede dieser Kisten zu einem zentralen Geschäft bringen. Ein Läufer oder jemand vom Fließband muss zum zentralen Lager gehen, um die benötigten Teile zu holen, und sie zurück zu ihrem Verwendungsort bringen. Das ist viel Zeit, die für eine Aufgabe mit geringem Wert aufgewendet wird, anstatt Komponenten zusammenzubauen.
Ein weiteres positives Ergebnis, das häufig auftaucht, ist die Identifizierung von Möglichkeiten zur Kostensenkung durch die Konsolidierung der Menge an Teilenummern, die Ihr Unternehmen kaufen, verwalten und handhaben muss. Wenn wir die Beschaffung von Teilen vereinfachen können, indem wir die Anzahl der Teile oder Lieferanten konsolidieren, die sie bereitstellen, oder sie als Kit liefern, müssen Sie weniger Stellfläche und unterstützende Ressourcen verwenden, die dann anderen hochwertigen Aufgaben zugewiesen werden können .
Eine Empfehlung, die wir häufig empfehlen, ist die Einrichtung von Regalen in der Nähe Ihrer Verwendungsorte mit hohem Volumen, damit Ihre Bediener weiterarbeiten können, anstatt in jeder Schicht hin und her zu gehen, um Teile zu holen.
Jedes Gespräch bringt neue Ideen hervor, schafft bessere Denkprozesse und etabliert eine offene Kommunikation zwischen den Partnern. Der One-Line-Walk wiederum legt den Grundstein für wertvolle Besuche in den kommenden Jahren.
Optimas-Kunden sind daran gewöhnt, unsere Teammitglieder in ihrer Werkstatt zu sehen, da Line Walks ein natürlicher Bestandteil unserer Servicebeziehung sind. Viele haben im Rahmen ihres Vertriebsprogramms sogar einen eigenen Optimas-Ingenieur vor Ort. Andere sagen oft: „Ihr seid meine Verschlüsse. Steigen Sie hier ein und helfen Sie uns, einige Änderungen vorzunehmen.“
Als Full-Service-Distributor kann Optimas Ihre Lieferkette näher zu Ihnen bringen. Anstatt bei vielen Lieferanten einzukaufen, von denen einige im Ausland ansässig sind, was mit langen Vorlaufzeiten einhergeht, helfen wir Herstellern, ihre gesamte Investition in Befestigungselemente ganzheitlich zu betrachten.
Tricks und Handwerkszeug
Da viele Kunden keine einfache Möglichkeit haben, auf ihre neuesten Stücklisten für Teile zuzugreifen, empfehlen wir oft die Implementierung einer internen Teiledatenbank mit Teilenummern, Beschreibungen und Zeichnungen, dies reduziert die Verbreitung von SKUs und Lieferanten und bietet ein einziges Repository für notwendige Abweichungen darin der Befestigungskategorie.
OptiTech-Lösungen Verwenden Sie die neueste Technologie, um die Bestandsauffüllung zu automatisieren, um Kunden Zeit und Geld zu sparen und Konsistenz zu gewährleisten. Hersteller müssen nicht mehr jeden Tag jemanden durch die Anlage schicken, um Teile in Behältern zu zählen, oder daran denken, Teile nachzubestellen, bevor (oder wahrscheinlicher, wenn) sie ausgehen.
Unsere Ingenieure verwenden SolidWorks 3D-Druck für das Prototyping und zur Verbesserung von Form, Passform und Funktion vorgeschlagener oder bereits verwendeter Teile. Wir nutzen auch BoltCalc, ein Programm von Bolt Science, das entwickelt wurde, um Verbindungssimulationen für Drehmomentspannung und Teilelebensfähigkeit bereitzustellen.
Im Produktionszyklus sind Verbindungselemente nicht immer gut dokumentiert. Aus verschiedenen Gründen weichen die verwendeten Teile von den Spezifikationen ab. In diesen Fällen können wir eine Teil-zu-Druck-Überprüfung durchführen, indem wir die Drucke des Unternehmens erhalten, die Teile überprüfen und das Design mit der Realität vergleichen.
Linewalk einrichten.
Der Line Walk ist der erste Schritt, um größere Probleme zu erkennen und anzugehen. Und bei einer Kaufentscheidung im Wert von mehreren Millionen Dollar, die mehr als 6 Monate dauern kann, ist es extrem riskant, KEINEN Line-Walk früh im Prozess durchführen zu lassen. Wenn ein Lieferant Empfehlungen abgibt, ohne Ihre Einrichtung zu besuchen, ist es nur Theorie und Produktion, Finanzen und Moral können darunter leiden.
Auch heute noch senden einige Unternehmen ihre Teilepakete per E-Mail an mehrere Lieferanten und wählen den niedrigsten Preis statt den größten Wert. Das bedeutet, dass sie nicht die Fragen stellen, die vor, während oder nach einem Line Walk auftauchen. Einfache, aber wirkungsvolle Fragen wie „Müssen wir wirklich jedes dieser Befestigungselemente verwenden oder könnten wir weniger, bessere Befestigungselemente verwenden?“
Ein qualitativ hochwertiger Line Walk erfordert Wissen und Planung seitens des Herstellers und seines Partners. Der Nutzen sollte immer darin bestehen, Organisationen dabei zu helfen, Kosten zu senken und die Effizienz zu steigern.
Wenn Sie mit Ineffizienzproblemen zu tun haben, wissen Sie wahrscheinlich, dass Veränderungen bevorstehen, unabhängig davon, ob Sie bei Ihrem derzeitigen Lieferanten bleiben oder nicht. Wenn Sie Lieferunterbrechungen oder leistungsschwache Teile hatten oder Ineffizienzen beobachtet haben, die die Produktion verlangsamen, ist es wahrscheinlich an der Zeit, Ihren Lieferanten von Verbindungselementen zu überdenken. Und es ist an der Zeit Planen Sie einen Line Walk mit Optimas.