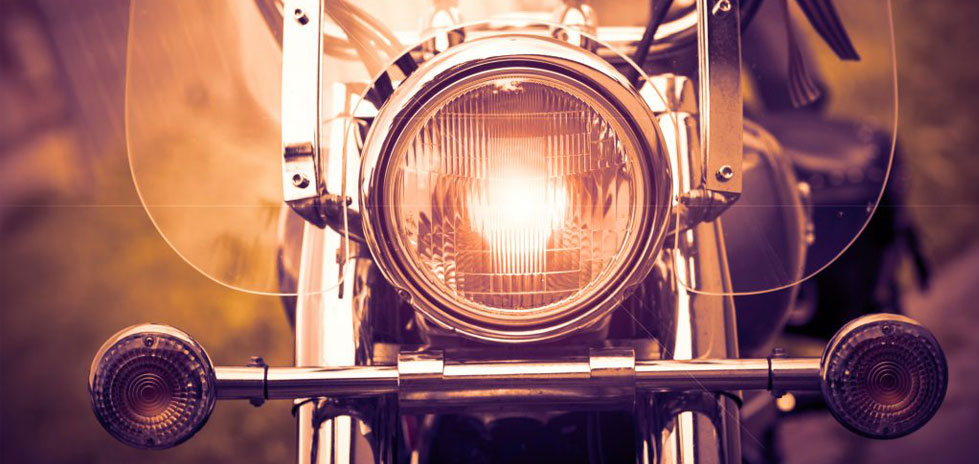
Anpassung, Qualität und Geschichte: Die Befestigungsanforderungen einer Prestige-Motorradmarke
Die Erfüllung der einzigartigen und oft herausfordernden Komponentenanforderungen einer legendären Motorradmarke ist eine feine Balance. Wenn das Aussehen, der Klang und der Geruch eines neuen Fahrrads bei Enthusiasten den perfekten Akkord treffen müssen, muss selbst das kleinste Detail perfekt sein. Das Management von Kosten, Leistung und Ästhetik von Verbindungselementen während eines Prototyping-Projekts ist immer eine Herausforderung, aber das Ethos der Marke muss berücksichtigt werden. Glücklicherweise wurde dieser Balanceakt vom globalen Befestigungsexperten Optimas perfektioniert.
Die Bewältigung dieser etwas gegensätzlichen Bedenken hat dazu geführt, dass Optimas eine 30-jährige Beziehung zu diesem speziellen Hersteller aufgebaut hat – wo ein kundenspezifischer Ansatz der Schlüssel zum Erreichen von technischer Exzellenz ist.
Die Definition von Befestigungsrichtlinien ist während der Prototypenentwicklung besonders schwierig, da die Vorstellung des fertigen Fahrzeugs, ganz zu schweigen von seinen endgültigen Komponenten, einer Vorhersage der Zukunft gleicht. Typischerweise konzentriert man sich auf die Standardisierung von Komponenten – das Auffinden bereits vorhandener Teile, die die technischen Anforderungen erfüllen. Darüber hinaus müssen Teilenummern zur Vereinfachung der Spezifikation konsolidiert werden. Dieser Ansatz dient dazu, Kosten in der Stückliste zu senken, Einsparungen, die sich durch jede Iteration des Prototypfahrzeugs noch verstärken. Was aber, wenn das Fahrzeug eine vorgegebene Markenästhetik erreichen soll? Wie senkt man effektiv die Kosten für einen Hersteller, der darauf abzielt, Fahrzeuge zu produzieren, die alles andere als die Norm sind? Der grundlegende Ansatz muss sich weiterentwickeln.
Diese Weiterentwicklung des Ansatzes ist Chris Sterner, Engineering Program Manager von Optimas, sehr vertraut: „Wir arbeiten mit dieser Marke zusammen, um die Richtlinien für Verbindungselemente zu definieren, wenn sich das Design noch im Clay-Model-Stadium befindet, was bedeutet, dass wir vollständig in die Design- und Engineering-Teams integriert sind vom Anfang an. Optimas fungiert als Berater für Befestigungselemente, wobei jede Mutter oder Schraube dem empfohlenen Design hinzugefügt und schließlich aus unserem globalen Komponentenportfolio geliefert wird. Für diesen Hersteller sind die fertigen Motorräder jedoch wie industrialisierter Schmuck. Abgesehen von den üblichen Überlegungen zur Kostenreduzierung und möglicherweise zur Gewichtseinsparung muss jedes Verbindungselement gut aussehen.“
Chris arbeitet als Verbindungsexperte zwischen den Einkaufs- und Konstruktionsteams des Herstellers. Seine Aufgabe besteht darin, die Stückliste (BOM) mit den technischen Anforderungen des Projekts abzugleichen. Derzeit liefert Optimas Komponenten an drei Produktionsstandorte in den USA, wobei sich ein großes Team ausschließlich um den Kunden kümmert.
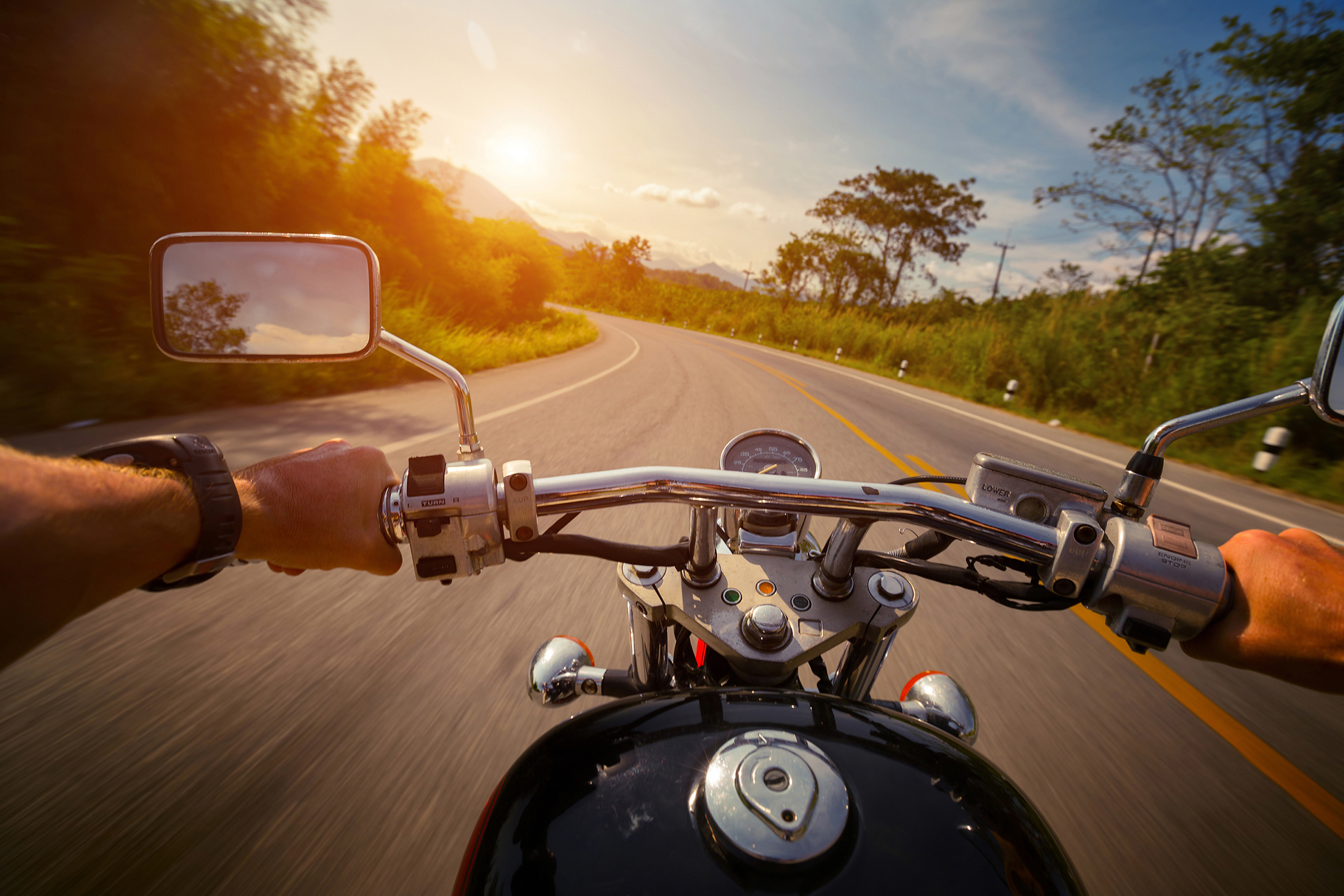
Fahrer, der Motorrad auf der leeren Asphaltstraße fährt
Wenn die Ästhetik für das fertige Produkt von entscheidender Bedeutung ist, ist die Anpassungsfähigkeit an die Anforderungen des Herstellers der Schlüssel. [Bildquelle: iStock/mihtiander] In einigen Fällen ist es vorzuziehen, bestehende Befestigungslösungen aus dem Optimas-Portfolio für eine kostengünstige Lösung zu empfehlen. Die Unterstützung von Ingenieuren bei der Identifizierung geeigneter Komponenten aus einer vorhandenen Stückliste, anstatt neue Verbindungselemente zu beschaffen, ist ein wichtiger Service, der die Komplexität der Lieferkette reduziert und die Kosten verwaltet. Wenn jedoch die Ästhetik für das fertige Produkt von entscheidender Bedeutung ist, ist die Anpassungsfähigkeit an die Anforderungen des Herstellers von entscheidender Bedeutung.
„Ein solches Beispiel sind die Zylinderschrauben mit Innensechskant, die bei dieser Motorradmarke verbaut sind“, führt Chris aus. „Diese Komponenten gehören zu den stärksten auf dem Markt und entsprechen der Markenethik, ein robustes Fahrzeug zu produzieren. Diese Komponenten sind jedoch für Werkzeugmaschinenhersteller konzipiert und nicht vollständig für die Ermüdungsanforderungen an ein Straßenfahrzeug geeignet. Was vom Hersteller gefordert wurde, existiert einfach nicht, also mussten wir als Lösung ein maßgeschneidertes exklusives Bauteil liefern. Um einen Kompromiss zu finden, liefern wir eine kundenspezifische Lösung mit der exakten Geometrie, um die Markenästhetik zu bewahren, aber auch eine erhöhte Duktilität in der Anwendung zu bieten, um das Leben auf der Straße zu überstehen.“
Optimas ist in der Lage, diesen Service aufgrund eines globalen Komponentenportfolios anzubieten, das Hersteller von Hochleistungsbefestigungselementen umfasst. Mit der Unterstützung eines globalen Netzwerks ist Optimas in der Lage, kundenspezifische Teile mit erhöhter Agilität zu liefern, ein Vorteil, wenn man bedenkt, dass ein Teilemangel jeglicher Art für einen OEM-Hersteller für einen reibungslosen Betrieb katastrophal sein kann. Ein Premium-Hersteller kann komplexe Bestellungen mit kurzen Vorlaufzeiten aufgeben – aber mit dieser Infrastruktur kann Optimas sich immer auf die Lieferung verlassen. Die Fähigkeit, „Magie geschehen zu lassen“, hat nur dazu beigetragen, die Beziehung zwischen OEM-Hersteller und Partner für Verbindungselemente zu stärken.
Diese starke Partnerschaft hat dazu geführt, dass Optimas an einigen vertraulichen und einzigartigen Projekten beteiligt war. „Ein besonders bemerkenswerter Auftrag umfasste einen PS-starken Rennradmotor, einen deutschen Sportwagenhersteller und ein Wochenend-Barbecue“, vertraut Chris an. „Der Hersteller hatte einen unglaublich leistungsstarken Fahrradmotor für den Einsatz in seinem Rennprogramm entwickelt und einige Erfolge auf der Strecke erzielt. Die Ingenieurteams stellten jedoch die Frage, ob die Einheit auf einem Straßenmotorrad verwendet werden könnte. Nach einigen Forschungs- und Entwicklungsarbeiten, die während eines Grillabends am Wochenende mit vielen Kabelbindern und Ersatzteilen durchgeführt wurden, war klar, dass das Konzept möglich war.“
Die Beteiligung von Optimas an dem Projekt begann in dieser Phase, als die OEM-Ingenieure eine Liste mit ungefähr 100 Teilenummern lieferten. Angaben wie bevorzugte Kopfformen, Materialqualitäten, Plattierungen und Festigkeitsklassen wurden jedoch nicht gemacht. Außerdem waren die Teile metrisch, als Zollmaße die Herstellernorm waren. Das Optimas-Team musste während des gesamten Projektverlaufs Richtlinien für Verbindungselemente definieren.
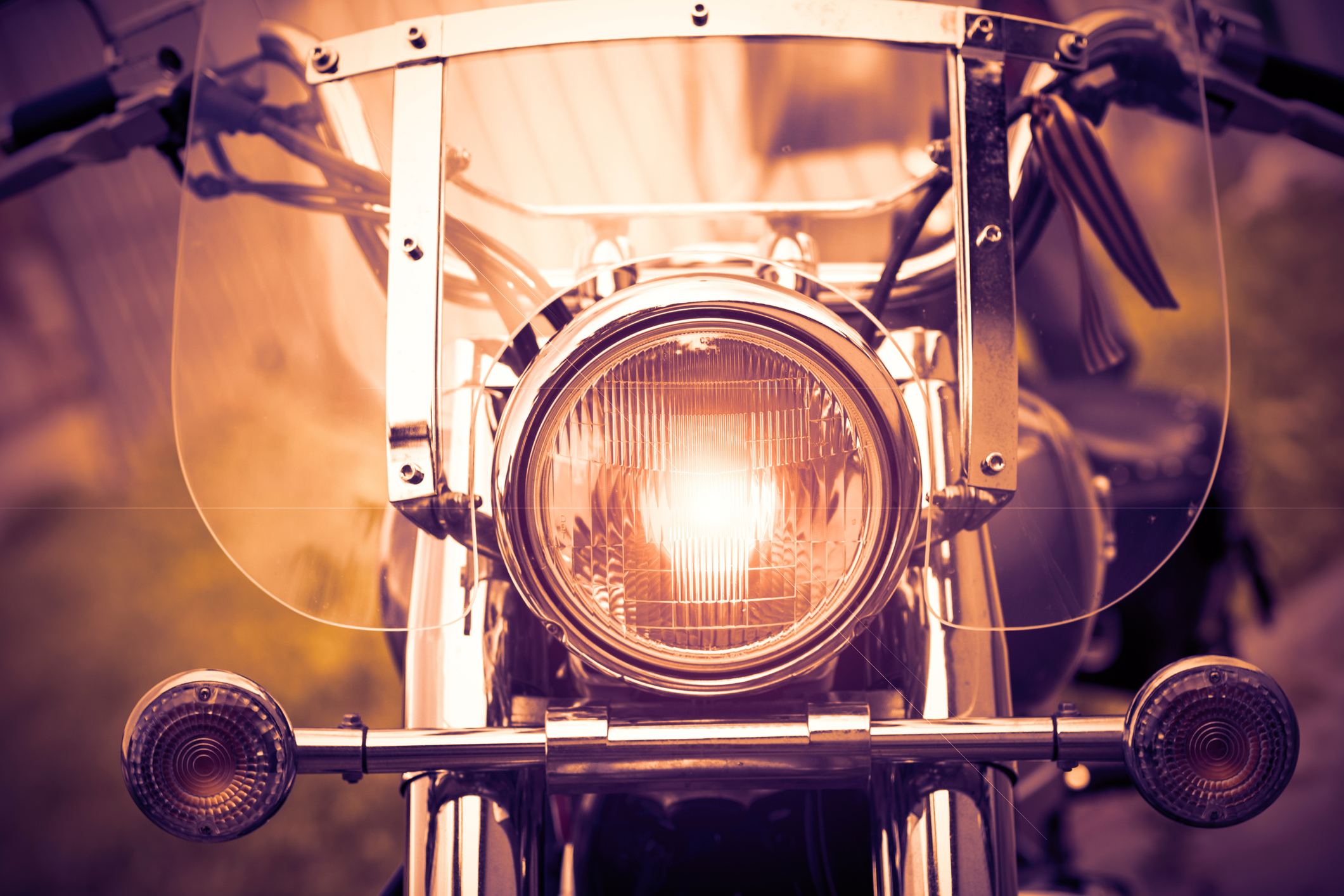
Scheinwerferlampe Motorrad. Blendenfleck
Wenn das Aussehen, der Klang und der Geruch eines neuen Fahrrads bei Enthusiasten den perfekten Akkord treffen müssen, muss selbst das kleinste Detail perfekt sein. [Bildquelle: iStock/Donyns] Chris fährt fort: „Eine weitere Herausforderung für den Hersteller bestand darin, den Motor straßentauglich zu machen. Als Rennmotor ist er darauf ausgelegt, ein paar Kilometer bei Vollgas zu überstehen – auf einem Rennrad muss er zwischen den Serviceleistungen viele tausend Kilometer laufen. Sie nahmen schließlich die Hilfe einer deutschen Sportwagenmarke in Anspruch, um den Motor zu modifizieren. Optimas war auch in dieser Phase wieder stark involviert. Unser Team reiste nach Deutschland, um bei der Spezifikation von Verbindungselementen für die Antriebsstrangmontage zu helfen. Anschließend haben wir die Ingenieure dazu gedrängt, so viel wie möglich Standardartikel zu verwenden und gleichzeitig die gleichen Festigkeitstoleranzen wie die ursprünglich von den Ingenieuren vorgeschlagenen kundenspezifischen Teile zu bieten.“
Das Streben nach Standardisierung brachte dem Hersteller in den fünf Jahren der Forschung und Entwicklung für das neue Modell enorme Kosteneinsparungen. Einige Kosten für einzelne Komponenten wurden um bis zu 75% gesenkt, ein Aufwand, der sich im Laufe des Projekts auf fast $2 Millionen an jährlichen Einsparungen allein bei Befestigungselementen belief. Trotz der Komplexität und Einzigartigkeit des Projekts war Optimas in der Lage, die Interessen des Engineerings und der Kosteneinsparung gleichzeitig in Einklang zu bringen.
Optimas hat ein Gleichgewicht gefunden zwischen Kosteneinsparungen durch Standardisierung und gleichzeitiger Vielseitigkeit und einem tiefen Verständnis dafür, was diese spezielle Motorradmarke auszeichnet. Durch die Abstimmung dieser Bedenken in Zusammenarbeit mit den Einkaufs- und Ingenieurteams des Herstellers war Optimas von der ersten Vorstellung an jedem neuen Modell an beteiligt. Während ein globales Komponentenportfolio und eine enge Beziehung dies erreicht haben, ist es die Fähigkeit, sich nahtlos an die unterschiedlichen Anforderungen des Herstellers anzupassen, die es ermöglicht, diese Premium-Motorräder entgegen allen Erwartungen auf wirklich kostengünstige Weise zu liefern.