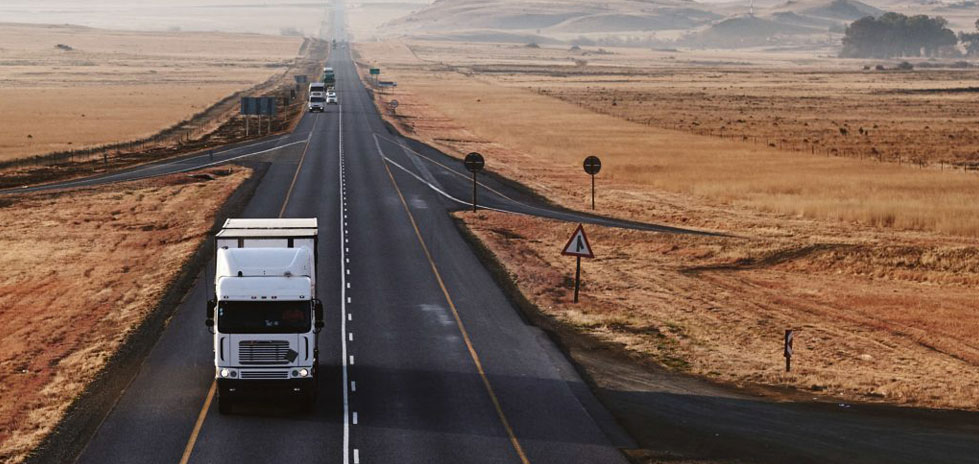
Komponentenwert hinzufügen: Zusammenschluss für die Lkw-Industrie
Die Auswahl eines Verbindungselements, das sowohl für eine Anwendung geeignet als auch wirtschaftlich ist, erfordert oft einen Spagat zwischen beiden Zielen. Bestimmte Spezialisierungen wie erhöhte Haltbarkeit, reduziertes Gewicht oder hohe Temperaturbeständigkeit erschweren den Auswahlprozess weiter und führten in einem bestimmten Fall zur Konstruktion eines hochentwickelten und teuren Kabelbinders für ein Dieselmotor-Emissionssystem. Als eine neue Innovation entdeckt wurde, sprangen die Experten für Befestigungslösungen von Optimas ein und stellten die Lösung bereit.
Die Auswahl eines Verbindungselements, das sowohl für eine Anwendung geeignet als auch wirtschaftlich ist, erfordert oft einen Spagat zwischen beiden Zielen. Bestimmte Spezialisierungen wie erhöhte Haltbarkeit, reduziertes Gewicht oder hohe Temperaturbeständigkeit erschweren den Auswahlprozess weiter und führten in einem bestimmten Fall zur Konstruktion eines hochentwickelten und teuren Kabelbinders für ein Dieselmotor-Emissionssystem. Als eine neue Innovation entdeckt wurde, sprangen die Experten für Befestigungslösungen von Optimas ein und stellten die Lösung bereit.
Optimas ist ein Experte für Verbindungselemente und Lieferketten, der weltweit tätig ist, um die Anforderungen der Hersteller an Komponenten zu erfüllen. In enger Zusammenarbeit mit den Kunden während der vielen Phasen der Entwicklung neuer Produkte und der Fortsetzung der gesamten Produktion bieten die Ingenieure von Optimas das neueste Wissen über Verbindungselemente, um die Stücklistenkosten (BoM) zu minimieren und die Produktionseffizienz zu maximieren. Diese kontinuierliche Verbesserung führt zu Einsparungen während des gesamten Produktlebenszyklus, baut starke Beziehungen auf und erfordert eine enge Kommunikation zwischen dem Kunden und dem Engineering-Team von Optimas. Als Optimas also eine neue Technologie entdeckte, die bei einem führenden Hersteller von Dieselmotoren große Kosteneinsparungen bringen konnte und die nur die Änderung eines einzigen Kabelbinders erforderte, hörte der Kunde zu.
Der fragliche Kabelbinder wurde verwendet, um Rohre und Kabel an mehreren Stellen des Abgassystems des Kunden zu befestigen, das Dieselmotorabgase reinigt und filtert, um den Ausstoß schädlicher Emissionen zu reduzieren. Der Reinigungsprozess innerhalb des Systems erfordert eine sehr hohe Hitze, etwa 200 °C (400 °F), und diese Komponenten könnten Temperaturen sehr nahe daran erreichen. Als kritische Eigenschaft dieser Komponente wurde vom Kunden eine Temperaturbeständigkeitsanforderung von mindestens 170 °C (338 °F) genannt.
Edelstahlkabelbinder wurden als eine Option angesehen, aber ihre scharfen Kanten schnitten nachweislich in die gebündelten Rohre und Drähte, und die Teile wurden früh in den Versuchen disqualifiziert.
Eine andere Option, die zur Lösung des Problems ausgewählt wurde, wurde aus Polyetheretherketon (PEEK) geformt, einem ultrahochhitzebeständigen Polymer mit einer Temperatur von 260 °C (500 °F). Dieses Produkt war eine Standardkomponente aus dem globalen Komponenten- und Lieferantenportfolio von Optimas mit Premiummarken. Unsere Lieferantenpartner aus der ganzen Welt werden auf der Grundlage ihres Fachwissens ausgewählt und ermöglichen die Spezifikation einer Standardlösung aus ihrem umfangreichen Angebot für eine sehr spezielle Anwendung.
Obwohl ein PEEK-Kabelbinder gut für die Anwendung bei hoher Hitze geeignet ist, ist er schwierig zu formen und extrem hart für Spritzgussmaschinen. Die resultierenden Kosten für jeden Kabelbinder betrugen etwa $3,50 bis $4. Obwohl dieser Preis im Vergleich zu einem normalen Kabelbinder aus Nylon sehr hoch ist, entsprach er dem des alternativen Kabelbinders aus Edelstahl. Also wurde der PEEK-Kabelbinder in Produktion genommen.
Ungefähr ein Jahr nach Produktionsbeginn und nachdem über 1 Mio. Teile verwendet worden waren, markierten die $3,5 Millionen, die für diese eine Komponente ausgegeben wurden, sie im technischen VAVE-System von Optimas als Kandidat für Änderungen.
Nach einer vollständigen Überprüfung der Anwendungsanforderungen haben die Ingenieure von Optimas andere verfügbare Optionen bei unseren Kabelbinderpartnern recherchiert und auch die jüngsten Innovationen untersucht, die eine kostengünstigere Lösung bieten könnten. Ein brandneuer Tefzel-Kabelbinder wurde gefunden, und obwohl das Material eine etwas geringere Temperaturbeständigkeit als der PEEK-Kabelbinder hatte, 356 °F (180 °C), lag es über den Mindestanforderungen, die für das Emissionssystem erforderlich sind. Da das Material viel einfacher zu formen war, waren seine Kosten weniger als halb so hoch wie die der PEEK-Krawatte. Es wurde auch festgestellt, dass die neonblaue Farbe der Tefzel-Krawatten eine viel attraktivere, moderne Ästhetik bot als die matt bräunlichen PEEK-Krawatten. Durch diese verbesserte Farbgebung wurde auch die Hightech-Optik des kompletten Abgasreinigungssystems weiter verstärkt, was sich beim Kunden als beliebter Zusatznutzen herausstellte.
Nach dem Test und der Implementierung in das neue Projekt lieferte der Tefzel-Kabelbinder im ersten Produktionsjahr eine jährliche Einsparung von $1,1 Millionen im Vergleich zur ursprünglichen Komponente. Seit seiner Einführung hat der neue Riegel dem Kunden allein in dieser Anwendung fast $3M eingespart. Sein Erfolg wurde auch auf neue Anwendungen und Modelle übertragen und gilt als technischer Standard, Best Practice und Design.
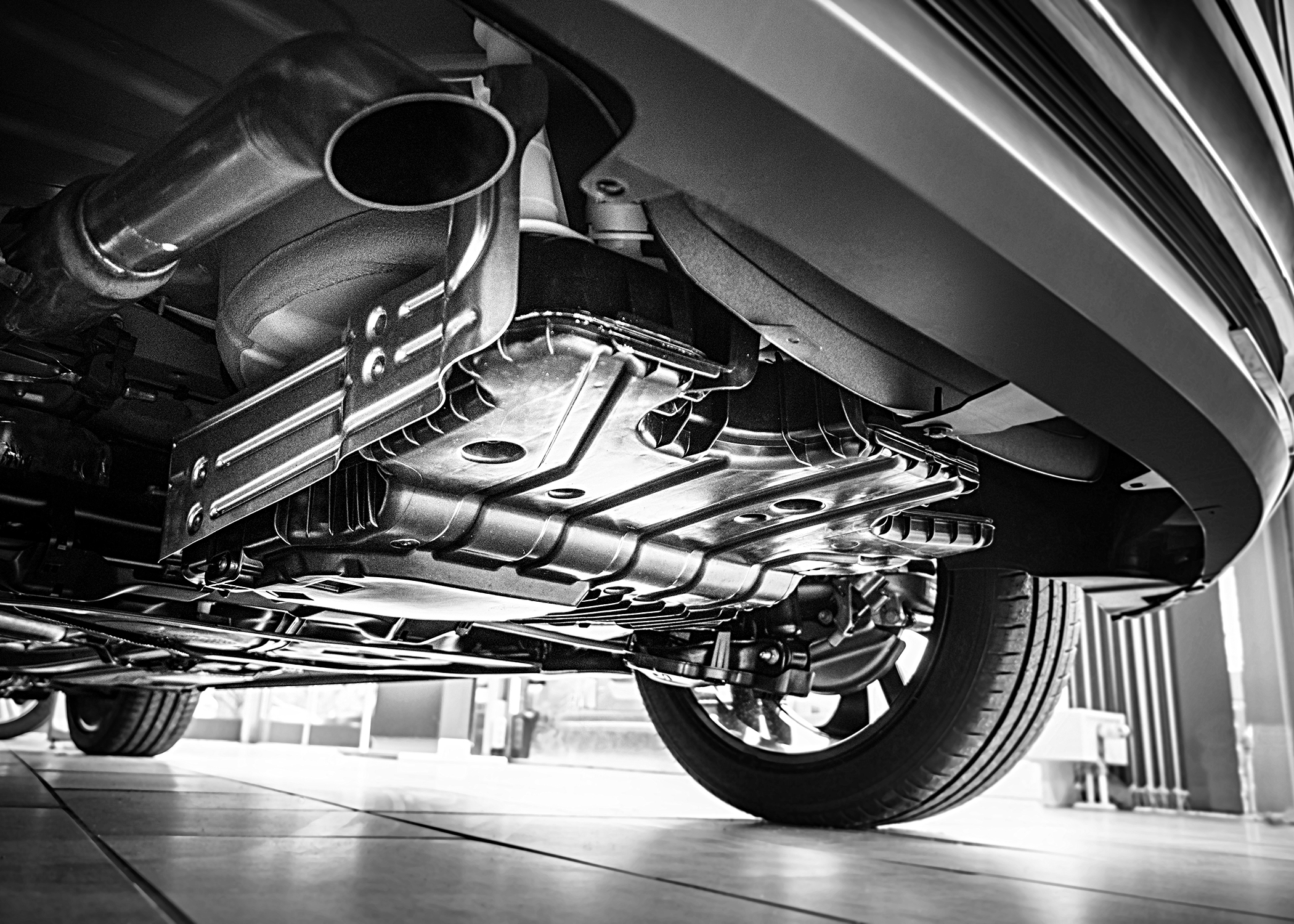
Unter einem Auto
Nach diesem Erfolg suchte Optimas nach anderen aktuellen Benutzern unserer PEEK-Kabelbinder in unserem weltweiten Kundenstamm, um die Einsparmöglichkeiten zu teilen. In der Dieselmotorensparte des oben genannten Kunden für Emissionssysteme wurde ein guter Kandidat gefunden. Leider zeigte das Tefzel-Material nicht die für diese Anwendung erforderliche Temperaturbeständigkeit, es entstand jedoch eine weitere Materialinnovation, Polyaryletherketon PAEK, das bis 200 °C (392 °F) verwendbar ist und die Anforderungen an die Motorleistung erfüllt. Durch erneutes Wechseln dieses einzelnen Kabelbinders konnte die Motorenabteilung weitere $300.000/Jahr harte Kosteneinsparungen erzielen.
Kosteneinsparungen dieser Größenordnung für Fertigungsbetriebe zu erzielen, ist nicht immer möglich, insbesondere wenn es um Verbindungselemente geht. Die Anforderungen an Verbindungselemente sind unterschiedlich, und potenzielle Kosteneinsparungen müssen immer gegen die Eignung für die Anwendung abgewogen werden. Mit einem sachkundigen Verbindungspartner mit einer Fülle bestehender Lösungen von einer Vielzahl globaler Partner und der Fähigkeit zur Anpassung können jedoch spezifische Verbindungslösungen bereitgestellt werden, die eine echte Wirtschaftlichkeit bieten. Während kundenspezifische oder innovative Komponentenlösungen oft teurer sind; Das Fachwissen und das gemeinsame Wissen der von Optimas angebotenen Lieferkettenpartner stellen sicher, dass die besten Komponenten zu den niedrigsten Gesamtkosten angeboten werden.