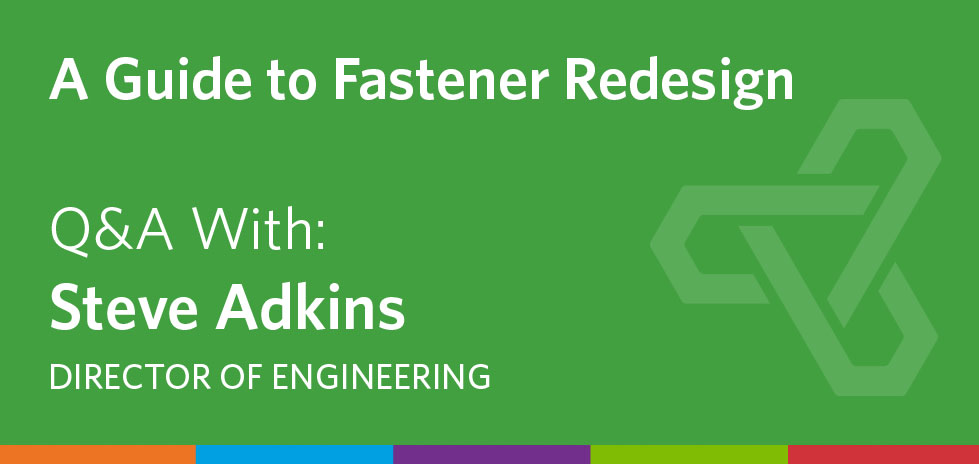
Optimas Unveils It’s Secrets: A Comprehensive Guide to Fastener Redesign
Fasteners play a critical role in holding together structures ranging from automotive products to wind turbines. However, there are times when fasteners don’t meet performance standards and require redesigning.
Steve Adkins, Director of Engineering at Optimas Solutions, a leading fastener manufacturer/distributor and service provider, explains that redesigning fasteners is a complex process that requires a thorough understanding of the current design’s performance expectations, operating conditions and potential design flaws.
During a question-answer session, Adkins delved into the critical factors that need consideration for a fastener redesign, including performance standards, environmental conditions, design defects, and available resources and technologies.
Can you walk through the process of redesigning fasteners?
Redesigning fasteners requires a thorough understanding of the problem and goals for the redesign. The process involves determining the requirements of the fasteners, brainstorming potential design changes and evaluating the manufacturability, aesthetic value and price of each design. The best solution is then chosen and tested before being implemented in production. Monitoring the performance of the new fastener during testing and making further refinements, if needed, is essential to ensure the re-design performs better for users and the company.
When do manufacturers decide to redesign fasteners?
There are several reasons why a manufacturer decides to redesign fasteners and some of them include:
- Changes in application or environment in which fasteners are used
- Need to improve performance
- Update design on a current model
- A desire to reduce cost and/or improve efficiency
What are some of the common performance requirements that fasteners fail to meet?
Nuts and Bolts: Some of the most common performance requirements that they fail to meet include inadequate strength grade, poor plating that results in corrosion or rust and hydrogen embrittlement that can cause the fasteners to break under stress. Additionally, thread issues and poor production quality can lead to the fasteners failing to meet their intended purpose.
Washers: Common problems include inadequate plating, hydrogen embrittlement, incorrect material selection and manufacturing issues. Fittings also often fail to meet material and manufacturing requirements.
What are the environmental factors affecting fastener performance?
Environmental factors such as temperature, humidity, exposure to corrosive chemicals and UV exposure can all affect the performance of fasteners. It is essential to consider these factors when redesigning fasteners.
How do you identify design flaws in fasteners that need to be addressed in a redesign?
BoltCalc is a valuable tool in diagnosing material and performance flaws in fasteners that need addressing in a redesign. It allows us to theoretically calculate clamp load and torque by adding variables such as plating, material, and other inputs. Using this software allows Optimas engineers to identify potential issues prior to production.
By using this software, engineers can ensure the new fastener meets the products’ necessary performance requirements.
What tools/analyses are available to redesign a fastener?
There are various tools and analyses available to identify and redesign a fastener, including computer-aided design (CAD) software like SolidWorks, BoltCalk for fastener analysis and assembly tools to install the fastener.
Optimas also has a wide array of testing equipment in our Wood Dale, IL and Columbus, IN facilities. This integrated approach enables engineers to test anything from tensile strength, plating thickness and even small screw drives to name a few.
What are the cost implications of a fastener redesign and how can savings be achieved through the redesign process?
Cost implications can vary and will depend on the manufacturer’s requirements. These can include reducing quality issues, speed of manufacturing and material that expands the fastener and product’s useful life. Also, cost-saving can be achieved by changing the fastener design and characteristics to better meet real use-case requirements.
What materials and technologies are available for use in fastener design?
There are several technologies available for use in fastener design such as CAD software and 3D printing materials — standard nylon to metal printing, non-ferrous metals for electrification and materials for high heat.
Are there any emerging trends, tools, or technologies in the fastener industry that could impact the redesign process?
The fastener industry is constantly evolving. Automation, new thread and drive designs, nut shapes and sizes, non-ferrous material for EV applications, non-torque related assembly processes (Huck) and assembling tooling for small fasteners are a few of the areas where fastener innovation is taking place every day.
What are the assembly and installation requirements for fasteners and can they be simplified or streamlined through a redesign?
Assembly and installation requirements can impact the efficiency and cost of installation and manufacturing processes. There are one-sided drive systems which can reduce labor on the assembly line and other non- torque drive products. These fasteners are usually more expensive but reduce quality issues, usually install faster and deliver repeatable clamp loads.
Also, depending on the critical nature of the fastener, the diameter and grade can be reduced to save weight. Rationalization and/or consolidation programs can be completed to reduce the number of fasteners in a product too.
How can fastener weight and size be reduced without compromising their strength and performance?
Weight and size can be reduced through design. For example, moving to lightweight materials, such as going from steel to plastic. An example of steel to plastic could be in non-structural rivet applications.
In larger bolted applications, working with the manufacturer to understand the application, using Boltcalc and even requiring durability testing are a few ways to verify weight reduction projects.
What testing and validation processes will be used to ensure the redesigned fastener meets performance requirements?
Various testing and validation methods, such as tensile testing, torque testing, vibration testing and environmental testing can be used. These tests evaluate performance and durability under different conditions and ensure that they meet industry standards. In addition to these testing processes, user feedback and data also are crucial in the fastener redesign process.
Conclusion
To ensure safety and performance and achieve production cost reductions, a fastener redesign may be the right move. With the right tools, materials and experts, this process can lead to significant improvements and cost savings.
To better understand if it’s time for a fastener redesign, let’s talk. You can reach me with this link.